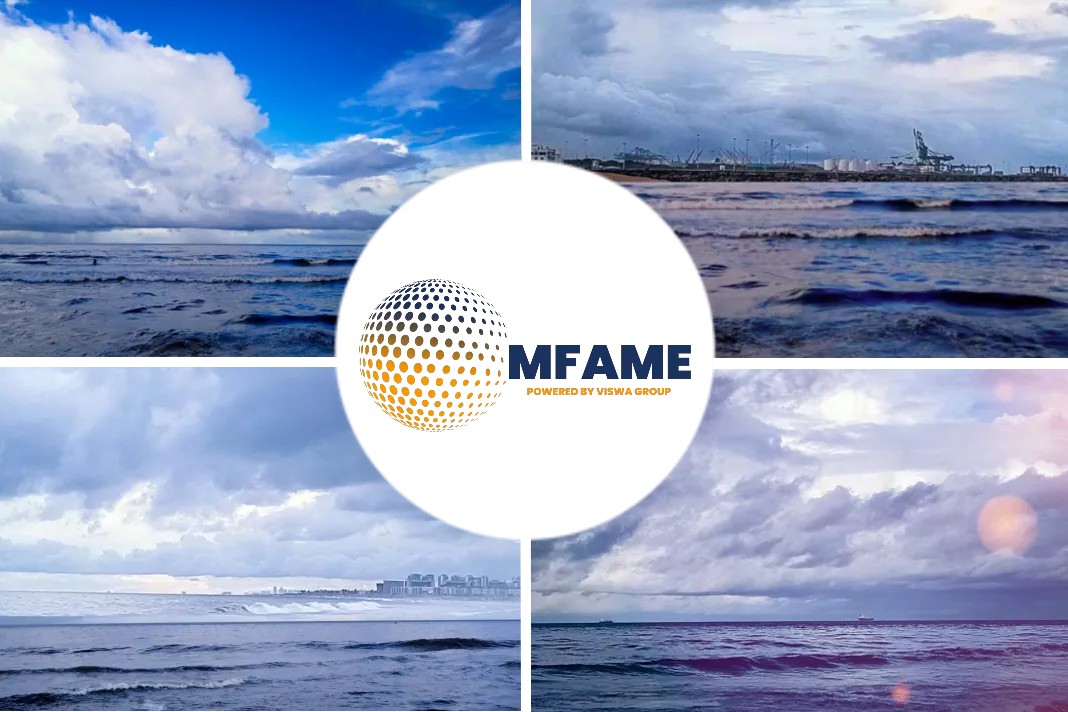
- Supply chain disruptions are easing, but the perception of risk remains.
- Performance at North American container ports fell by almost 50% from Q2 2020 to Q3 2022.
- Geopolitical risk must be factored in following Russia’s invasion of Ukraine and rising tensions over Taiwan.
- Great risk and unpredictability will drive decisions on inventory and manufacturing.
Supply chain risk, low before the pandemic, emerged highly elevated and likely to remain that way for several years to come. The implications are significant. Elevated supply chain risk for corporations managing long-haul, transcontinental supply chains means a greater risk of delay and less predictability in end-to-end ocean transport transit times. That, in turn, will result in longer product development and manufacturing lead times, higher inventory levels and greater use of airfreight, which can be up to 70 times the cost of ocean freight on a per-unit basis, reports SP Global.
Fundamental Change Since Pre-COVID-19
The decade prior to the pandemic saw a series of disconnected but, compared with COVID-19, relatively minor shocks to the containerized supply chain. After a disruptive six-month stretch of longshore labor unrest affecting U.S. West Coast ports in late 2014 and early 2015, normal flows resumed. They normalized again after the 2016 bankruptcy of Korea-based Hanjin Shipping, then the world’s seventh-largest container line, which idled 96 ships and $14 billion of goods worldwide.
They did so yet again following a surge of goods in late 2018 as U.S. retailers rushed to get Chinese-made products into the country ahead of the 25% duties threatened by the Trump administration, set to take effect Jan. 1, 2019. While those shocks created short-term delays, supply chains in the aggregate were largely unaffected.
Disruption Went From Periodic to Constant
COVID-19 marked a radical change to that dynamic. Disruption, instead of being periodic, became constant. With each new shock to the containerized system — record volumes, historic port backups, successive China lockdowns, Suez Canal blockage, inland North American rail service suspension — the disruption was compounded.
Productivity at North American container ports was a case in point. According to S&P Global Market Intelligence, performance at North American container ports fell by close to 50% in the two-year period from Q2 2020 to Q3 2022 (see chart 1). In early 2020, ports were moving an average of 56 containers for every hour a ship needed to spend in port. Now they move an average of fewer than 30 per hour, despite recent improvements as volumes have declined.
Performance at North American container ports fell by almost 50% from Q2 2020 to Q3 2022.
Chart 1
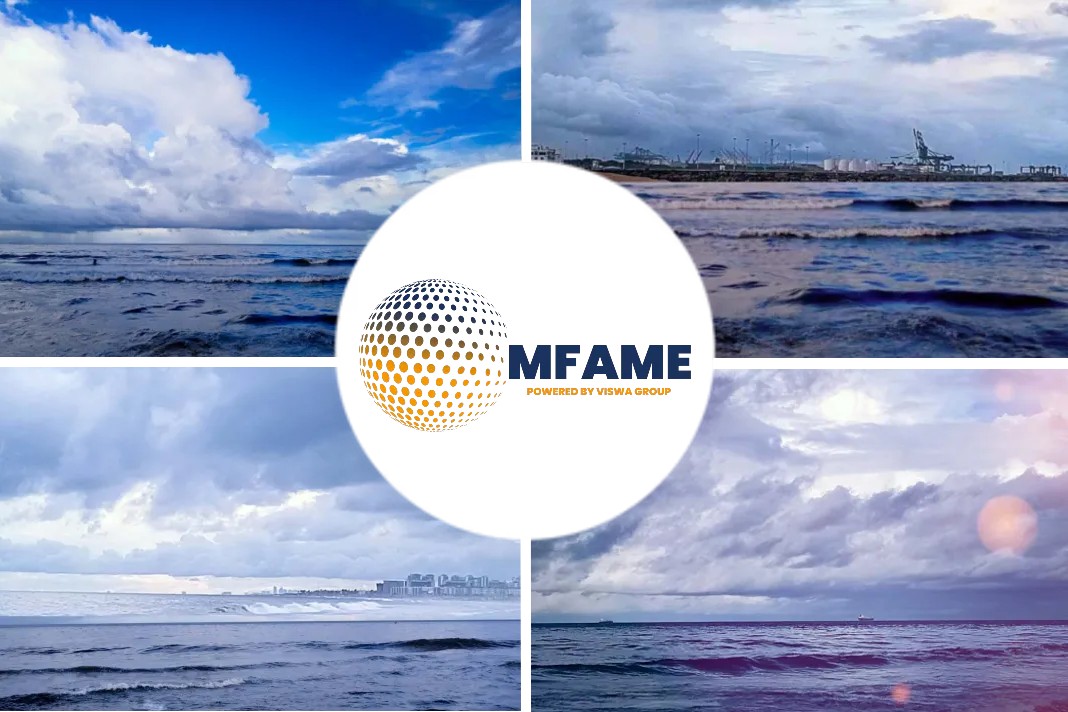
It is the unfamiliar aftermath of that experience that corporate leaders and logistics teams will be grappling with in 2023 and for years beyond. Although port and end-to-end transport delays are easing, trust in the supply chain has been damaged. Given that there are multiple new risk factors on the horizon, it is hard to envision trust in the system being restored to pre-COVID-19 levels any time soon.
That reality will lead to difficult decisions for corporate leaders, who will be forced to maintain higher just-in-case inventory levels and to plan longer product lead times, increasing risk by elongating the time between product design, inventory planning and when those goods become purchases. On the other hand, new technologies such as 5G, edge computing, artificial intelligence, blockchain and machine learning will improve decision-making and the predictability of supply chains in the future.
It is hard to envision trust in the system being restored to pre-COVID-19 levels any time soon.
Supply Chains Face Multiple Types of Risk
This elevated supply chain risk is coming from multiple directions. China’s path forward on its COVID policy is not yet clear, which will continue to pose the risk of future lockdowns and manufacturing disruptions. Geopolitical risk, rarely part of the supply chain calculus, must be factored in following Russia’s invasion of Ukraine and rising tensions over Taiwan; 40% of total U.S. containerized imports originate in mainland China, according to S&P Global Market Intelligence, and diversification of sourcing including “friendshoring” will accelerate through 2030, which is a risk factor in itself. Climate change is increasing the frequency of severe weather events that disrupt cargo movements.
Such transport and logistics risks will continue to rise. In the U.S., virtually no new port capacity is being created, despite expectations for continued containerized trade growth. A marine terminal that opened at Charleston, S.C., in 2021 was the first new facility in the U.S. in over a decade. Longshore labor opposition to cargo-handling automation means ports have limited ability to improve productivity. Attempts to encourage round-the-clock operations at ports to expand de facto capacity have met with minimal success. Efforts to share data to improve overall cargo movement are in the early stages. The result is that any unanticipated cargo surges, which have always occurred periodically, will almost automatically hit a wall of capacity and lead to delays.
The conclusion is clear: Although supply chain risk was considered minimal or immaterial pre-COVID-19, going forward it will define how supply chains are organized and executed. Technology will play a greater role as companies seek to minimize the impact of a painful and costly transition.
Did you subscribe to our daily Newsletter?
It’s Free! Click here to Subscribe
Source: SP Global