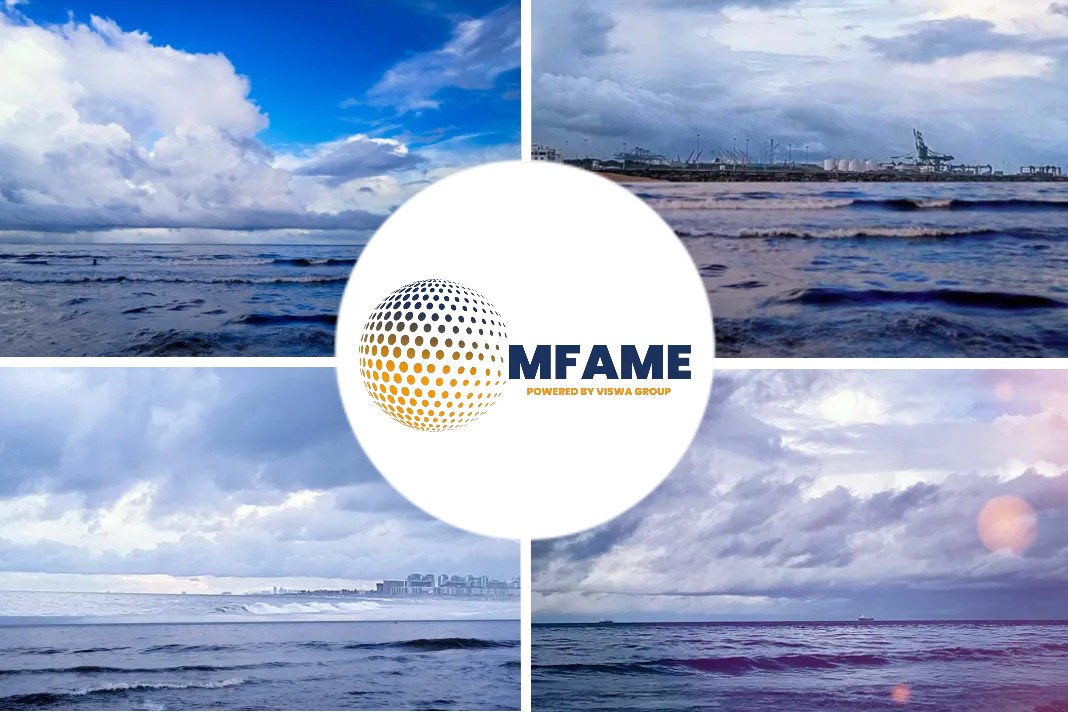
Slow steaming offers economic and environmental rewards, but not without sacrifices, reveals a Manifold Times news source.
Slow steaming
Slow steaming is often considered the easiest solution for overcoming both economic and environmental challenges.
However, doing so without risking the safety and long term efficiency of ships needs careful consideration by ship owners and operators, shares Nicea Ng, Marine Technical Specialist, Innospec Limited.
“Every vessel has an optimum engine load where the combustion is almost complete and the SFOC (Specific Fuel Oil Consumption) is at minimum level,” states Ng.
“When an engine is running on a low load condition, the cylinder pressure and temperatures are lower which leads to poorer ignition and incomplete combustion of bunker fuel.
“Though reducing speed offers a better CII rating; this may also lead to energy and combustion efficiency losses that cause preventable damage to vessel machinery.
“Vessels with high engine output will need costly retrofit solutions with high CAPEX in order to permanently work at lower loads.
“From experience, slow steaming usually results in a variety of negative effect on vessel engines.”
Adverse effects of slow steaming on ship engines
Poor Atomisation
Higher volume of fuel trapped at the injector tip (sac) delivering uncalculated fuel to the cylinder and increasing the likelihood of dripping. Increased fouling and carbon deposits all contribute to poor atomisation and subsequent drop in performance.
Poor Combustion Characteristics
At reduced ME load operation, inadequate turbo charger speeds are generated to provide adequate air to the combustion chamber, leading to lower combustion efficiency, unburnt fuel and the formation of harmful emissions.
Reduced Air Flow
Reduces engine efficiency and causes fouling in the air supply/scavenge system. Subsequently this can lead to very high differential and exhaust temperatures which can damage engine components and lead to burned exhaust valve as one example.
Cold Corrosion
Corrosive wear on the cylinder liners caused by acid condensation due to the drop in engine operation temperature caused by slow steaming operation.
Fouling Effect
On Turbocharger (turbine side),
- On Exhaust Gas Boiler (heat exchanger pipes)
- On Injector (clogged nozzles),
- On Piston rings (deposit accumulation – lack of sealing)
Smart slow steaming’ with Octamar™ Ultra HF & Octamar™ Complete – fuel treatment systems with Class Verification
Combustion catalysts have a positive impact on the fuel’s combustion profile by providing a faster and more complete combustion of regular fuel at any load condition.
With a significant reduction in uncaptured fuel energy, vessels have seen 2.1-3.9% fuel savings which have contributed to better CII ratings.
“Even till today, issues with slow steaming have remained the same. However, with new regulations and changes in fuel quality over the years, Innospec continues to improve its technology to optimise today’s marine fuel,” informed Ng.
“Octamar™ Ultra HF & Octamar™ Complete allows vessels to slow steam with associated benefits by minimising the adverse effects listed above while improving fuel consumption and emissions.”
The unique treatment package improves energy efficiency of ships by reducing ignition delay, cleaning injectors, and reducing afterburn to mitigate all the issues associated with slow steaming while decreasing combustion properties and early max heat release to maintain energy efficiency.
“ClassNK has also verified several trials conducted over a decade which demonstrated the active fuel consumption (2.1-3.9%) and emissions reduction of Octamar™ technology,” she highlights adding the Octamar ™ solution can be further included in vessels’ SEEMP III.
Note: Readers may contact Innospec Limited for more information on Octamar™ Ultra HF & Octamar™ Complete at: salesmarine-asiapacific@innospecinc.com
Did you subscribe to our Newsletter?
It’s Free! Click here to Subscribe!
Source: Manifold Times