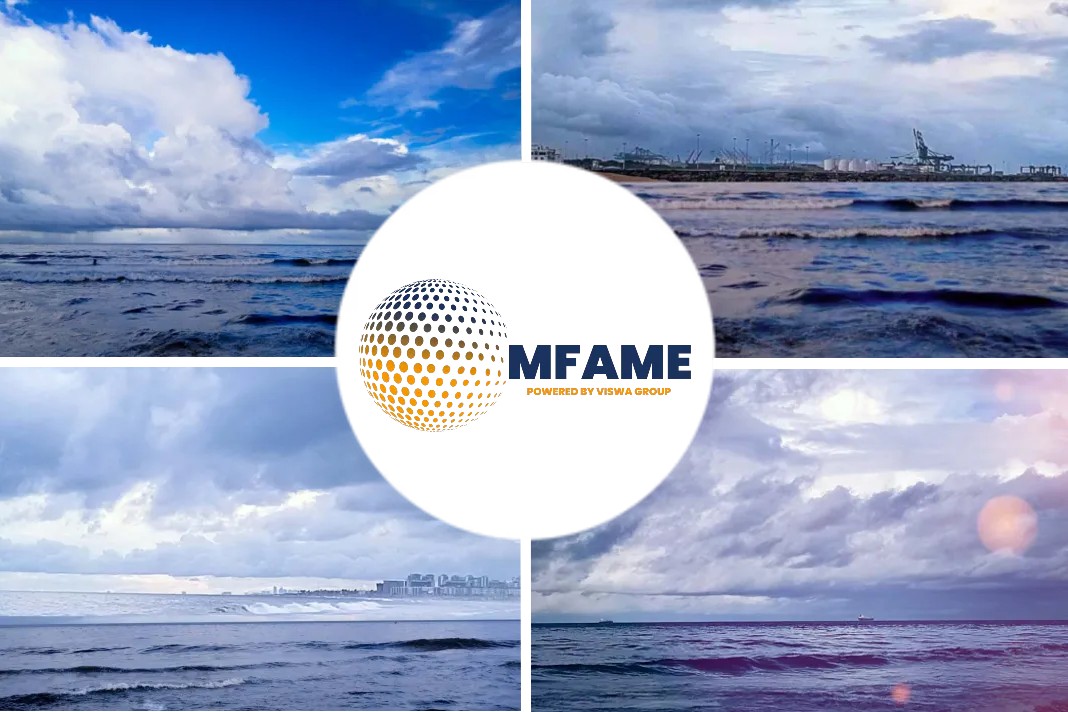
The changes in consumer behaviour over the last few years have created huge fluctuations in supply and demand. The buying frenzy of the pandemic years created supply shortages across every sector. In response, many businesses increased production. But the economic slowdown of the last 1-2 years meant a decrease in consumer demand, leaving businesses with excess inventory at every point in their supply chain, reports Maersk.
What is fulfilment technology?
Those quick pace changes have made it more critical than ever for businesses to have visibility into their fulfilment operations. They need to know where they have inventory and how it can be moved in order to adapt to changes in the supply chain.
Historically, ad hoc systems running across multiple supply chain partners have increased complexity and costs in fulfilment. To provide a higher level of operational excellence and reliability, the industry must invest in more optimised fulfilment technology.
Fulfilment technology is a broad category—it can be any combination of software, hardware and other technologies used to manage the process of order fulfilment. Simply put, it’s the technology ecosystem that gets your orders from the internet to your home.
Arguably, the biggest player in that ecosystem is the warehouse management system (WMS). A WMS serves as a central platform for all the activities within a warehouse: inventory management, order processing, picking and packing, shipping and receiving.
The average North American warehouse is about 2,300 square metres (about 25,000 square feet) — meaning that a system that maximises space utilisation, inventory accuracy, enhances productivity and reduces errors is key to giving customers visibility into their inventory and improving efficiency in their supply chain.
How we’re driving operational excellence with a standardised WMS
As our fulfilment footprint has grown to over 660 facilities in 66 countries with an 11 million square metre footprint, we found ourselves with different warehouse management systems for different markets, geographies, etc. These different systems made it challenging for us to scale both the experience we offer customers and the experience our operators have using the systems.
To improve operational efficiency, visibility for our customers and create a better experience for our employees, we’re now rolling out the One Maersk WMS. The new WMS is built on the LF Logistics WMS, which has been developed over 20 years based on deep customer input. We’re further building on that system by creating a consistent user interface (UI).
This single UI allows us to scale our WMS across sites, regions, cultures and languages. It means that across all 660 fulfilment centres, we use one piece of software with one user interface. The new UI uses universal design principles so it’s intuitive to use and easy to onboard new operators. It also allows operators to switch between fulfilment facilities without a steep learning curve. Ultimately, that means we can streamline processes, minimise waste and optimise our operations.
Did you subscribe to our daily Newsletter?
It’s Free! Click here to Subscribe
Source: Maersk