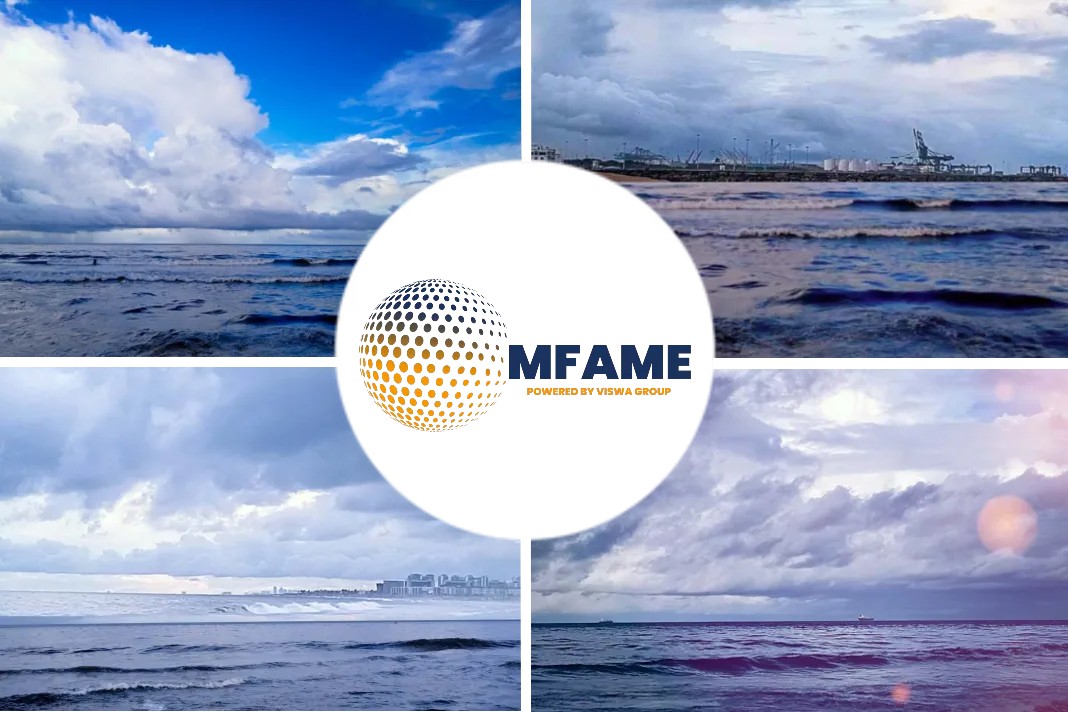
High-manganese steel aims to lower LNG cargo and fuel tank costs, writes John Snyder for Riviera news source.
Hanwha Ocean R&D Institute
Hanwha Ocean R&D Institute head details the drive behind the successful development and commercialisation of high-manganese steel Type B and Type C LNG tanks
Most LNG cargo and fuel tanks are made using IMO-approved 36% nickel steel (invar), 9% nickel steel, stainless steel and aluminium, but a new, less expensive, robust material — high-manganese steel — is gaining increasing attention.
While traditional IMO-approved materials have proven robust and safe for handling the rigors of LNG cryogenic storage, they are expensive, and their production is inefficient, resulting in high manufacturing costs. This, in turn, increases the cost of building LNG carriers and LNG-fuelled ships — two core high-value products of South Korean shipbuilders.
This led to South Korean shipbuilder Hanwha Ocean (formerly Daewoo Shipbuilding and Marine Engineering) and domestic steel manufacturer POSCO undertaking a joint development project (JDP) in 2010, examining the feasibility of using high-manganese steel as an alternative to these traditional materials.
Joining in the JDP were five leading class societies (ABS, BV, DNV, KR and Lloyd’s Register). The goal of the JDP was ambitious: to develop and commercialise LNG cargo and fuel tanks that exhibited the same or superior qualities of handling the stresses of cryogenic storage, while reducing material cost and improving productivity. Completed a decade ago in 2013, the JDP also had national significance for South Korea, a global leader in LNG carrier and LNG-fuelled ship construction.
“High-manganese steel is 30% cheaper than 9% nickel steel”
In a paper presented as part of a panel on Advances in LNG carrier design and LNG-fuelled ships at LNG 2023 in Vancouver in July, Hanwha Ocean R&D Institute head, Joong Kyoo Kang, detailed the findings of the JDP and the South Korean shipbuilder’s subsequent development and commercialisation of IMO Type B and IMO Type C fuel tanks using high-manganese (Hi-Mn) steel.
To evaluate high-manganese (Hi-Mn) steel, Hanwha Ocean compared its cryogenic performance to current materials, including 9% nickel steel, stainless steel, and aluminium used in LNG storage tank manufacture approved by IMO and listed in the International Gas Code (IGC) and International Fuel Code (IGF).
Under the three-year project, the JDP undertook several complex technical challenges. The shipbuilder developed high-manganese steel construction technology, fabricated mock-ups, performed cryogenic tests, designed cryogenic tanks, and evaluated safety.
Steelmaker POSCO developed Hi-Mn steel materials and welding materials, while the class societies provided engineering support and material approval, conducted cryogenic tests and devised mock-up inspections.
In his paper, Mr Joong Kyoo Kang noted several attempts to commercialise Hi-Mn steel for cryogenic applications had been made in other countries but had failed due to the difficulty in producing steel without defects. One of the major reasons for failing to produce sound steel was the difficulty in developing the correct welding materials.
Using various fatigue tests, Hanwha Ocean in collaboration with POSCO was able to develop and improve welding materials suitable for each welding process. The JDP was completed in 2013.
One of the key takeaways noted by Mr Joong Kyoo Kang was that using Hi-Mn steel in the manufacture of the LNG tanks can achieve a weight reduction through reduced thickness, compared to other materials with similar low-temperature strength. This yielded improved productivity and increased competitiveness through material savings.
Additionally, its low coefficient of thermal expansion compared to other low-temperature materials reduces thermal stress caused by temperature changes in the LNG tank, making it superior in terms of design, he said.
POSCO reported its cryogenic Hi-Mn steel has globally high production rates and is relatively inexpensive. Besides noting its superior toughness and tensile strength compared to conventional materials, high-manganese steel is 30% cheaper than 9% nickel steel, according to the steelmaker.
“Hi-Mn steel is being examined for use in tanks for ammonia-powered ships”
The steel contains 22.5 to 25.5% manganese, maintaining excellent strength, even at cryogenic temperatures of -196 °C. Expectations are high in country that Hi-Mn steel will boost the competitiveness of several South Korean industries, from steelmaking to shipbuilding to LNG tank manufacture for land, vehicles and marine-based applications.
In 2018, IMO’s Marine Safety Committee approved interim guidelines for applying Hi-Mn steel in cryogenic LNG storage and fuel tanks. These guidelines outlined the requirements for designing and manufacturing Hi-Mn steel for LNG cargo and fuel tanks, ensuring compliance with IMO’s safety codes.
Hanwha Ocean has developed its own IMO Type B and C LNG tank designs, which are marketed under High Manganese steel Cargo Tank Independent Type- B (MCTIBR) and High Manganese steel Cargo Tank Independent Type-C (Mc-CR), respectively to distinguish them from existing IMO type B and C LNG tanks made of 9%-Ni steel.
Mr Joong Kyoo Kang noted general industry consensus was reached that IMO Type B tanks are the most effective and reliable solution for LNG fuel tanks for container ships because of their space effectiveness and structural robustness against sloshing. The featured characteristic of the Type B tank is the application of a partial secondary barrier instead of a full secondary barrier. This partial secondary barrier consists of a leakage path on the primary barrier, drip tray, and high-end verification engineering on the safety of the primary barrier, ie, tank boundary, against leakage.
Due to the comparatively more spacious open-deck area, IMO Type C tanks have been adopted for LNG fuel tanks in the LNG dual-fuel design of bulk carriers and very large crude carriers (VLCCs), one of the core ship types constructed by Hanwha Ocean. Working with a partner fabrication yard in South Korea, Hanwha Ocean developed a Hi-Mn IMO Type C independent tank.
The culmination of this 10-year development effort with POSCO has begun to bear fruit. According to Mr Joong Kyoo Kang, Hanwha Ocean has secured orders for its HiMN tanks for 36 LNG-fuelled ships, including orders for MCTIBR Type B fuel tank systems for 22 container ships and Mc-CR Type C fuel tank systems for 14 VLCCs. The first two VLCCs equipped with these Mc-CR Type C fuel tank systems were delivered last year.
Hanwha Ocean reported the first cube-shaped MCTIBR Type B fuel tank system was installed in a 24,000-TEU LNG dual-fuel container ship last year.
Hanwha Ocean also has plans to employ Hi-Mn steel beyond LNG. Mr Joong Kyoo Kang confirmed that Hi-Mn steel is being examined for use in tanks for ammonia-powered ships and for hydrogen carriers. It has been confirmed that high-manganese steel has high stability at the supercool temperatures required for liquefied hydrogen (-253°C) compared to the existing stainless steel. Based on various tests and studies, plans are being made to apply the results to a mock-up of a liquefied hydrogen tank for verification tests.
Did you subscribe to our daily Newsletter?
It’s Free! Click here to subscribe!
Source: Riviera