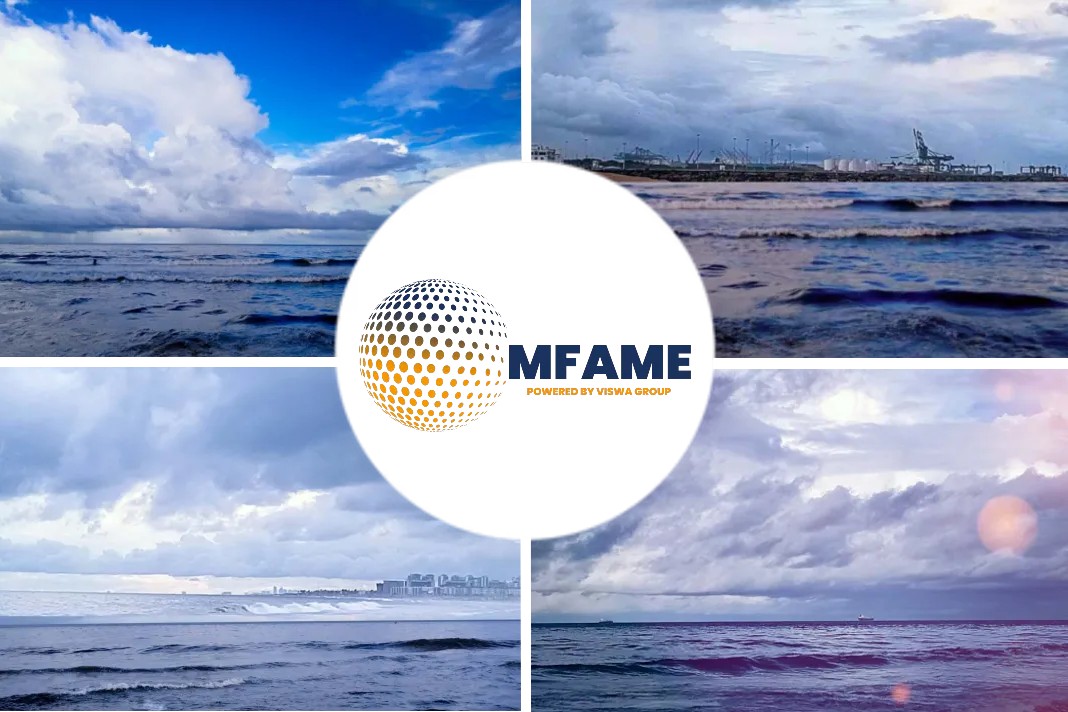
The National Transportation Safety Board (NTSB) has issued an investigation report, on the collision between Cargo Ship Damgracht and Cargo Ship AP Revelin.
The incident
On August 21, 2022, about 1045 local time, the cargo ship Damgracht was inbound in the Sabine Pass Outer Bar Channel en route to Beaumont, Texas, and the cargo ship AP Revelin was outbound when the two vessels collided near Port Arthur, Texas. There were no injuries to the Damgracht’s 16 crewmembers nor to the AP Revelin’s 19 crewmembers, and no pollution was reported. Damage to the AP Revelin was estimated at $3.4 million, and there were no reported damage costs for the Damgracht.
Analysis
With the abrupt loss of propulsion, while transiting at 15 knots, the Damgracht began veering to port into the path of the outbound AP Revelin, which was about a half mile away and was transiting about 10 knots.
The pilot aboard the Damgracht immediately took steps to notify nearby vessels and maneuver the vessel—he broadcast the loss of propulsion over VHF radio, directed the captain to sound the “danger” signal, and ordered the rudder hard to starboard.
However, he was unable to alter the vessel’s heading, since his rudder commands were unable to counter the vessel’s veering to port due to the lack of propeller wash passing over the functioning rudder and the disabled bow thruster.
Without a means for the pilot to maneuver the vessel, the Damgracht continued to head across the channel and into the path of the AP Revelin. Upon hearing the VHF broadcast, the pilot aboard the AP Revelin immediately took action to avoid the approaching Damgracht.
However, because there was only a half mile between the two vessels, there was not enough time for the AP Revelin pilot’s evasive actions to be effective in avoiding a collision. About 2 minutes after the Damgracht’s engine failure, its bow struck the port quarter of the AP Revelin.
The previous afternoon, the Damgracht’s main engine had alarmed (due to low cooling water pressure and high cooling water temperature) and shut down, causing a loss of propulsion. The crew anchored the vessel, and that evening, the engine crew cooled down the main engine, disassembled the no. 6 cylinder head, and found a failed cylinder head gasket.
When the cylinder head gasket failed, high-temperature, high-pressure gas likely escaped from the combustion chamber into the crankcase and into the cooling water system, reducing the effectiveness of the cooling system and causing the engine to overheat.
The gasket failure also likely allowed products of combustion and cooling water to leak into the cylinder from the cylinder liner’s cooling water passages and contaminate the engine’s lube oil system.
After the repairs, the crew used the engine’s cooling water system to preheat the engine and put online the lube oil purifier (with its heating system). The crew tested the engine for about 30 minutes and again opened the crankcase for inspection. The engine went through several temperature changes throughout the evening and following morning due to operational conditions during maneuvering, as well as being cooled for maintenance, operated for testing, cooled down for inspection, and then heated the morning before departure. Temperature changes can cause water vapor to condense and change back into a liquid and form droplets, which can collect in the lube oil sump.
Due to the ambient air conditions the engine was exposed to during repairs and cooling water that had likely leaked into and contaminated the lube oil from the failed gasket, it is likely that higher levels of water entered the crankcase than could be removed overnight by the lube oil purifier or evaporate from the heat of the running engine in the short time it was tested post repair.
When the OMD indicated a high oil density alarm during the casualty transit the following morning, the chief engineer verified that there were no elevated bearing temperatures or high crankcase pressure, opened the OMD measuring chamber cover, wiped the sensing glass, reset the unit, and restarted the engine. Any abnormalities or impurities on the sensing glass may have been an indication of actual high oil density.
However, the chief engineer found none while wiping the sensing glass; the main engine operated without incident after he restarted it, and the vessel transited without issue to the anchorage. Additionally, after the collision, routine maintenance was performed on the OMD, including cleaning, filter changes, and air pressure verification, and about 25% of the lube oil in the main engine sump was replaced.
The OMD was successfully tested, and no issues were reported. (Routine maintenance on the OMD had been completed 4 days before the collision with no issues reported.)
Therefore, it is likely that the OMD had triggered a false alarm after sensing water vapor that had condensed in the sample. The water vapor was likely present from cooling water that had entered into the lube oil system after the gasket failed the day before and from the ambient air conditions (high humidity) during the maintenance completed the previous evening to repair the gasket.
Conclusions
The National Transportation Safety Board determines that the probable cause of the collision between the cargo vessel Damgracht and the cargo vessel AP Revelin was the Damgracht’s loss of propulsion caused by an automatic shutdown of the main engine due to a false alarm, likely triggered by water vapor sensed by the oil mist detector shortly after engine maintenance was completed to replace a failed cylinder head gasket during high-humidity conditions.
Lessons learned
Oil Mist Detector Precautions After Engine Maintenance
When certain engine components, such as cylinder head gaskets, fail, cooling water can be introduced into engine lube oil systems. Ambient air conditions, such as high humidity or extreme cold temperatures, can also increase the water content within engine lube oil sumps.
The elevated quantity of water in lube oil systems can trigger false alarms in engine crankcase oil mist detectors (and lead to an engine shutdown) due to water droplets passing through the measuring track or the filter glass detecting condensation (mistaking it for oil mist).
After an engine’s crankcase is opened and exposed to these conditions during maintenance and repair, it is good practice for engine crews to inspect and test the lubricating oil system for water intrusion and ensure lube oil purifying equipment is functioning properly to remove any water or other contamination in the lube oil.
Did you subscribe to our daily newsletter?
It’s Free! Click here to Subscribe!
Source: NTSB