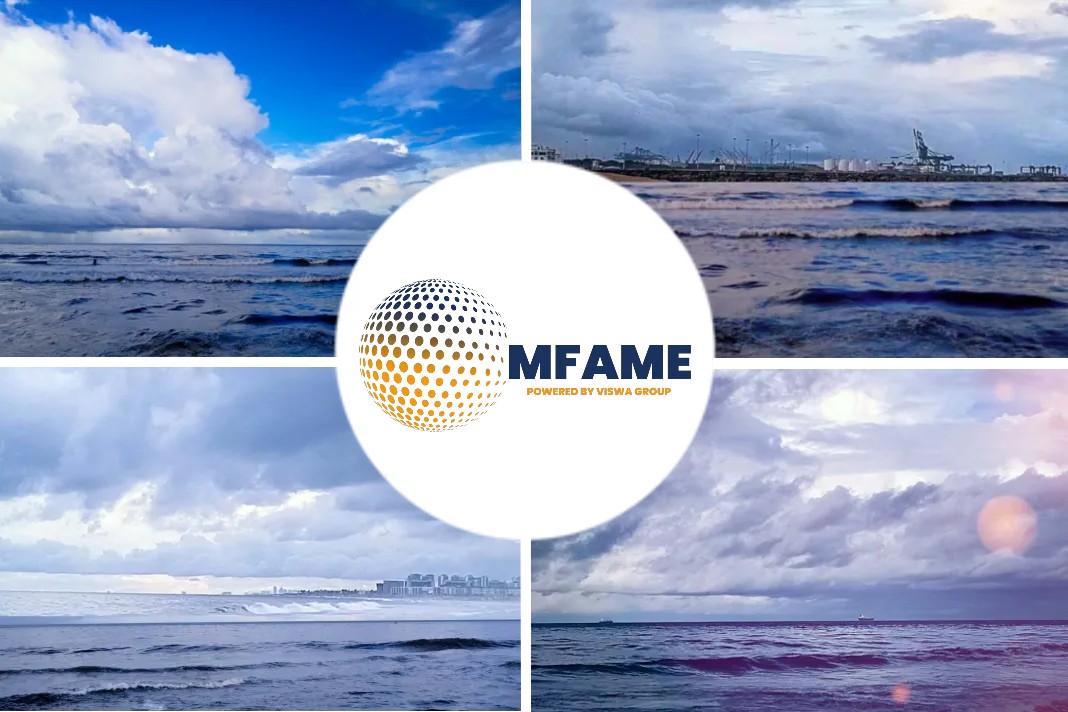
A lot of problems are created, because of improper treatment of fuel, and these can be avoided by paying attention to the lab analysis. Given below are 10 points marine engineers must check in the fuel oil testing report.
Density
The supplier, on completion of bunkering, gives a BDN( bunker delivery note), which has the density mentioned on it, but this is basically to determine the weight of fuel delivered, it might not be very accurate. The correct density is required for changing the gravity disc of the purifiers, to ensure correct purification. This is not required in the newer purification systems as they do not have a gravity disc.
Viscosity
HFO used to burn in marine engines has a viscosity of 380 cst, and for IFO it’s 180cst(This is at 50 deg centigrade). Generally, the viscosity required for combustion is between 13-15cst. But it can be different for different engines. In most ships, the viscotherm is automated, which means it continuously monitors the viscosity of the fuel going to the engine and accordingly regulates the temperature.
Water %
Fuel with high water content will burn less efficiently as the calorific value is reduced. The high amount of water in fuel is quite troublesome if the fuel is going to be kept for a long time in a bunker tank. Over a period of time, the water will settle at the bottom and cause problems while transferring.
Carbon Residue
It is the amount of carbon remaining when the fuel sample is completely burnt. It indicates the quality of the fuel. A higher carbon residue value means more deposits on piston land and fuel valve tips. It also means fuel oil has poor ignition quality, which causes ignition delay after burning. Avoid low-load operation when using such fuel. Or if they have to run on low load as most ships are now being run on lower rpm.
Sulphur Content
The most important value to be checked, for MARPOL regulations, especially when sailing in ECA areas. As of 1st January 2015, the sulfur content for fuel on ships sailing in the ECA area is 0.10% m/m. Also, it’s necessary to check sulfur content in the new intelligent engines, where the cylinder lubrication is done exactly as per the sulfur content of the fuel in use. High sulfur content leads to cold corrosion.
Vanadium and Sodium %
Vanadium is a metallic element found in crude oil. When it combines with sodium in the ratio of 3:1, it forms a low melting point compound which causes high-temperature corrosion and the formation of localized hot spots. This leads to the burning away of exhaust valves, seats and piston crowns. Although removing vanadium is difficult, it’s easier to remove sodium via purification and heating.
Flash Point
The flash point of all fuels used in the engine room should have a flash point greater than or equal to 60. This information will be presented by the supplier before bunkering, but it is always better to confirm this from the lab analysis.
Pour Point
The pour point is the minimum temperature at which a liquid ceases to flow. For pumping and handling purposes it is always good to know the minimum temperature to be maintained.
The above are the major points to be considered before using the newly bunkered fuel oil. In addition to this, labs may also conduct further additional tests such as total sediment, or for lead, phosphorus, calcium and zinc, which are indicators of the presence of waste lubricating oil, which sometimes may be added to the fuel. Always keep all equipment involved in the transfer and handling of fuel in good condition. Auto backwash filters are to be cleaned regularly and never in any condition to be bypassed.
Did you subscribe to our newsletter?
It’s free! Click here to subscribe!
Source: Marineinsight