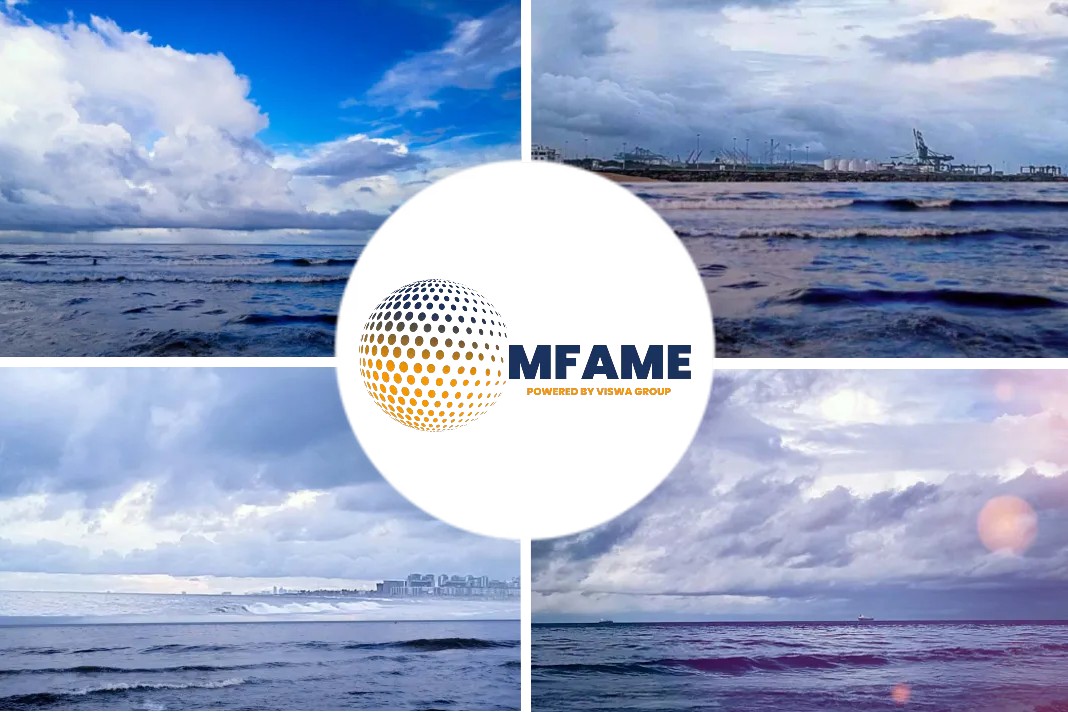
IMCA, in its latest safety alert, reports about the uncontrollable movement of auxiliary whip line.
What happened
When starting up, a vessel main crane started behaving in an uncontrollable and potentially hazardous way. The block and hook were hoisted up to the sheave, when the auxiliary wire parted due to the forces applied. The block and hook were ejected forward until they hit a stair railing, approx. 4m forward of the sheave. Then the block and hook fell approx. 3m down to deck and bounced before coming to rest. Six people were involved in the operation and found to have been at high risk had conditions been slightly different. Two crew were involved in un-hooking; three were in a nearby deck workshop with no barrier in place between them and where the block and hook landed, and the crane operator was in the crane cabin. When realizing something was wrong, the two personnel on deck quickly vacated the immediate area. No-one was harmed.
What was the cause
The main crane auxiliary line encoder unit was damaged due to water ingress, and gave the wrong input to the crane, causing uncontrolled movements of the auxiliary wire as the crane was started up.
What went right
After the incident there was an “All Stop” and “time-out for Safety” held. All personnel involved took part in a debrief and were looked after by the on-board medic – in the context of emotional and mental health rather than physical injury.
What went wrong
The door to the deck workshop was open with no barrier in place to the main deck, leaving the three persons in the workshop exposed to the risk of walking into a hazardous/line of fire area;
There was also additional risk for personnel not part of the operation to have accidentally being hit, as there were no barriers in place at the stairs from the mezzanine deck to the main deck.
What lessons were learnt?
Barriers should have been in place to prevent personnel from accessing the area;
Crane start up routine was not optimal leaving personnel exposed to uncontrolled movement;
The design of the old encoder did not provide drainage possibilities. The encoder was fitted in a sealed component housing and onboard vessel crew maintenance was not permitted.
Corrective/preventative actions
Repairs:
- The faulty encoder was replaced with a new encoder with drain plug;
- The crane was repaired and inspected by the crane manufacturer. In addition, an inspection by a competent and independent third-party expert was carried out;
- A safety bucket was installed on deck for the auxiliary crane hook. This will prevent use of anchor point which will then prevent need for personnel to un-hook at crane start up.
Procedures and risk assessments: The risk assessments and procedures for crane operations (including barriers) were reviewed and updated;
Members may wish to:
- Check their own lifting equipment to check for potential similarities related to crane type and encoder, such as exposure of encoder housing, degradation of unit, risk of water egress;
- Look into risks at crane start up, checking if personnel can be removed from hazard/line of fire area;
- Ensure barriers are in place to ensure personnel are kept out of line of fire zones, not only for deck operations but also for startup of crane and effects of crane failures, as applicable.
Did you subscribe to our newsletter?
It’s free! Click here to subscribe!
Source: IMCA