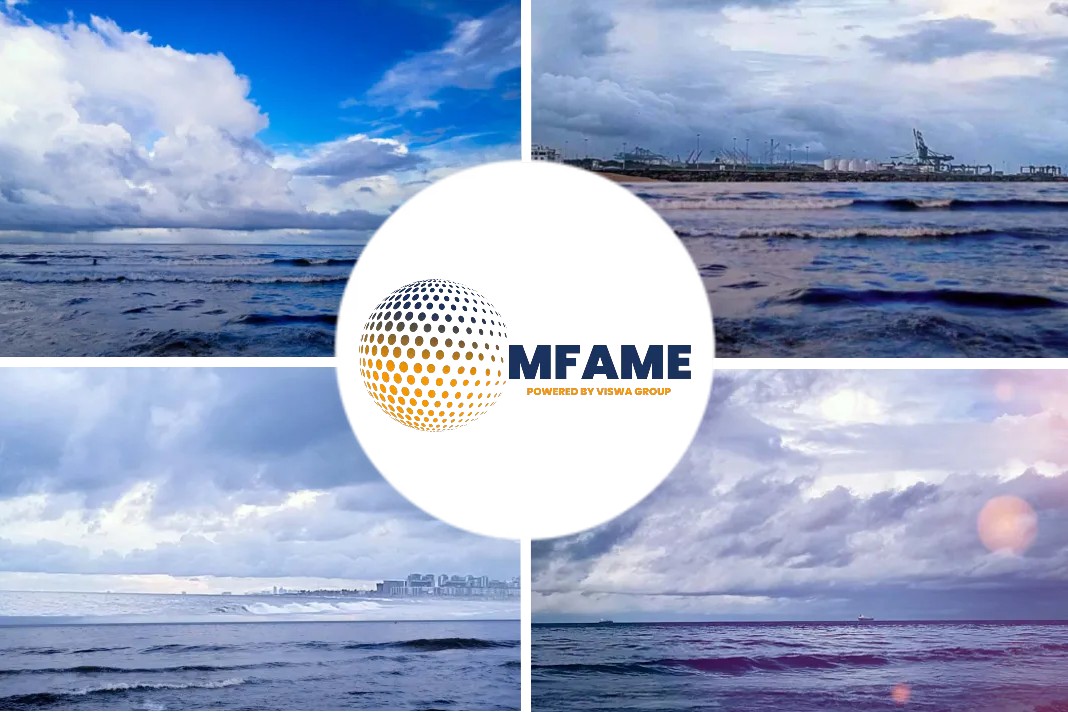
- A self-organizing ecosystem (SOE) is a collection of collaborating organizations that adapt to forces they experience or anticipate.
- Shipping is arguably the earliest large-scale SOE, and the industry is now considering the development of dedicated ammonia bunkering vessels.
- The challenge lies in the unique characteristics of ammonia, which requires larger quantities to be bunkered and requires special safety measures.
- An ammonia bunkering vessel would be equipped with a bunkering manifold with three liquid lines and two vapor lines on both sides of the bunkering vessel.
Bunkering ammonia not so dangerous after all? intrigues an Offshore Energy news source.
Ammonia bunkering vessels
Despite ammonia’s well-known toxicity, it has been successfully transported as cargo on LPG ships in recent years.
Now, the industry is eyeing the development of dedicated ammonia bunkering vessels. The challenge lies in the unique characteristics of ammonia: its low energy density demands larger quantities to be bunkered, and its potential hazards necessitate special safety measures.
Seeing that cryogenic fuels have been bunkered and well-tested in the industry, a similar concept is being considered for ammonia.
An ammonia bunkering vessel will be equipped with a similar loading arm to an LNG bunkering vessel. Nonetheless, it would require a significantly larger bunkering capacity, since vessels powered by ammonia would necessitate up to three times the amount of ammonia to achieve the same energy output as those using LNG or traditional fuels.
As such, the bunkering vessel would be fitted with a bunkering manifold provided with three liquid lines, instead of the usual one, and two vapor lines on both sides of the bunkering vessel, Prakash Chandra, Director of Hong Kong-based Fleet Management Limited, said in a recent webinar hosted by the Maersk Mc-Kinney Centre for Maritime Decarbonization.
The company has been working with SABRE Group in Singapore since 2021 on the development of ammonia bunkering infrastructure.
Ammonia-fueled vessels are expected to have a bunker manifold about midship, with one or more liquid lines and a vapor return line. The number of manifolds would depend on the size of the ship and its bunkering tank.
Current bunkering vessels have a maximum size of 10,000 cubic meters, but the new designs, for example for LNG bunkering vessels, are set to push boundaries, with sizes ranging from 24,000 to 32,000 cubic meters.
Prakesh’s team is already working on two vessel designs for an ammonia bunkering vessel, the smallest one with 24,000cbm, and the bigger with around 32,000cbm loading capacity.
However, larger quantities of ammonia come with the need for bigger equipment, larger/multiple hoses, and higher pumping rates.
What is more, the bunkering equipment needs to be redesigned so that the spill control equipment can handle larger volumes and toxic gas. That also means that special protection needs to be introduced in the manifold and bunkering equipment to detect and protect the crew from potential leaks.
In practice, this is expected to produce different ventilation arrangements and main vent mast when compared to conventional bunkering vessels and LNG bunkering vessels.
“The weak links are the connection points, which are manifolds and hoses, basically the points of transfer,” Chandra said.
“The manifold would need to be designed focusing on protection against spill and spread of ammonia vapors. We have been discussing the development of semi-enclosed bunkering stations where the leakage can be contained. This would be coupled with an alarm system, extraction fans, and water mist which would absorb ammonia vapors.”
The manifolds would be equipped with a large spill tray to contain the leak there, and a separate storage tank to contain ammonia mixed water in tanks.
Once the bunkering is finished, a purging process would be initiated so there are no emissions to the atmosphere, which means the vessel would also need to have a purge tank.
Handling hoses presents a critical concern, however, Chandra said that after conducting a study on the characteristics of hoses, it was found that bunkering hoses are robust and challenging to leak or burst, adding confidence in their safety.
Some of the recommendations of the study indicate that the hose to use for ammonia bunkering should be an 8-inch cryogenic hose, with a maximum permitted flow rate of about 1250 cbm per hour for ammonia. For safety reasons, during bunkering, the maximum rate permitted should be 1000 cbm per hour.
To meet the needs of large container vessels, up to three hoses could be used simultaneously with one vapor return line, Chandra noted.
An additional protection that would need to be introduced is an insulation sleeve (cryo-jacket LNG protection sleeve) which can be attached to the hose to prevent spray and the leak can be collected back to the drip tray.
Quick coupling and decoupling are not as dangerous as believed.
“There is a perception that when there is a quick release of hoses and bunkering equipment, a lot of liquid would be released. However, we tested this during Gastech Singapore and saw that the connections were seal-tight. Therefore, the perception that a quick decoupling would result in ammonia leak is not valid,” he further explained.
“Therefore, ammonia as of now is not looking so dangerous to be bunkered,” Chandra concluded.
“We are working now with MPA and the SABRE consortium to develop the bunkering procedure, training and handling all the risks by actually doing it and testing it.”
Did you subscribe to our daily newsletter?
It’s Free! Click here to Subscribe
Source : offshore-energy