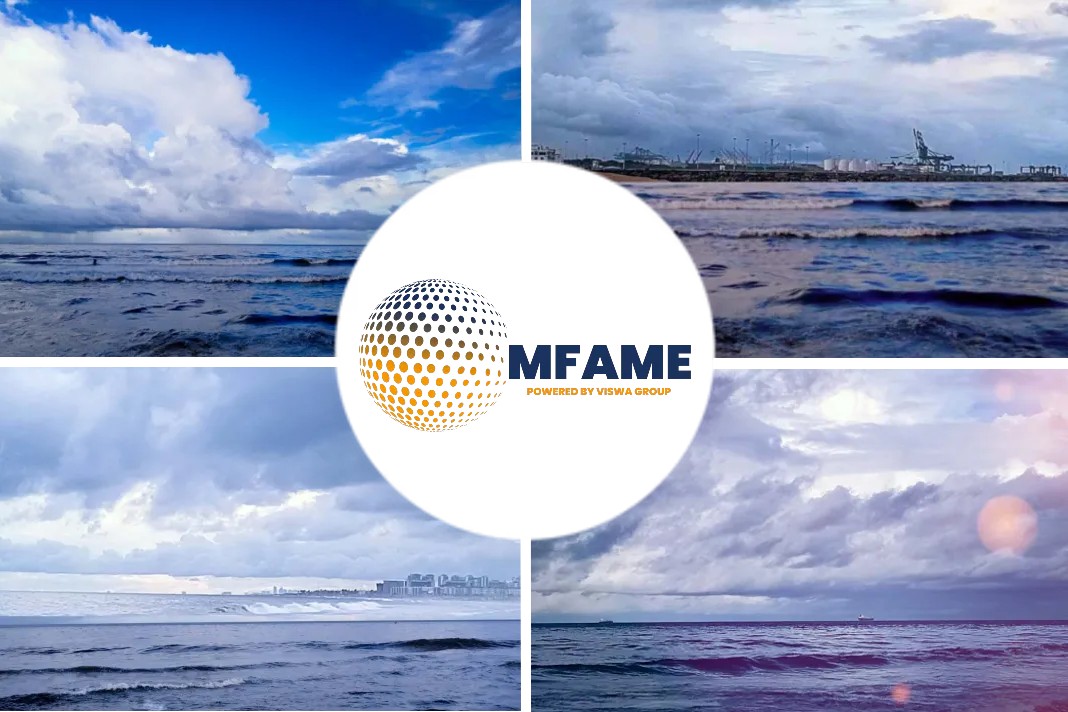
Kostas Alexis of the Autonomous Robots Lab, Department of Engineering Cybernetics at the Norwegian University of Science and Technology, explores the use of autonomous robotics for inspection operations.
Operations For The Maritime Sector
Let us consider, for example, the case of inspecting enclosed spaces for the maritime sector, such as ship ballast water tanks and cargo holds. With the world greatly relying on maritime transport and other marine structures, human surveyors must deal with a fleet involving more than 100,000 ships as per the “Handbook of Statistics 2022” of the United Nations Conference on Trade And Development. During such inspections, surveyors inspect within dangerous, confined, enclosed and GPS/GNSS-denied environments that are hard to access, difficult to traverse, with low-light and slippery surfaces, while some of the areas may have low oxygen levels.
Reflecting these challenges, the European Maritime Safety Agency reports many accident conditions even with anchored ships. Considering the above and other similar examples across application domains it comes as no surprise that robots have long been sought as the ultimate solution for automating inspections, eliminating risks for human personnel, and minimizing the associated costs, while also significantly reducing possible dead-time of the assets involved.
Limitations To The Use of Robotics
First, teleoperation or some other form of densely human-supervised methodology is typically still employed for the robots to execute inspections. Second, robotics for inspection operations are not always reliable, especially in the most challenging environments, which implies that human surveyors often must still be on-site. These factors limit the potential benefits offered by robotics for inspection operations. At the epicenter of solving the underlying technological challenges and enabling autonomy in diverse industrial inspections anywhere and subject to any conditions are two research directions, namely:
- Enabling resilient robotic autonomy: First and foremost, robots must operate autonomously in all applicable environments and conditions relevant to industrial inspection. Settings such as ship ballast water tanks, underground mines or oil and gas facilities present strenuous navigation challenges. Those areas are GPS/ GNSS-denied and often present sensor degradation (e.g., the presence of obscurants such as dust and smoke). At the same time, they involve geometries that are highly complex, often large-scale but also narrow, requiring multi-storey navigation and traversing through hard-to-access passages such as manholes. This calls for fundamental contributions towards resilient robotic autonomy.
- Facilitating semantically driven reasoning: Beyond the core necessity of resilient autonomy, inspection operations of high quality also require the transition from robots that “sense” and “map” the world to robots that also “reason” about it. Specifically, this refers to semantics-driven reasoning tailored to industrial inspection. This, for example, can enable a robot to reason that a certain structural component (e.g., a ballast tank web frame) necessitates specific inspection behaviors and has a specific relative value for the quality of an inspection. Such semantics must be detected, localized, and exploited by informed planning algorithms onboard the robotic systems.
Did you subscribe to our newsletter?
It’s free! Click here to subscribe!
Source: Openaccessgovernment