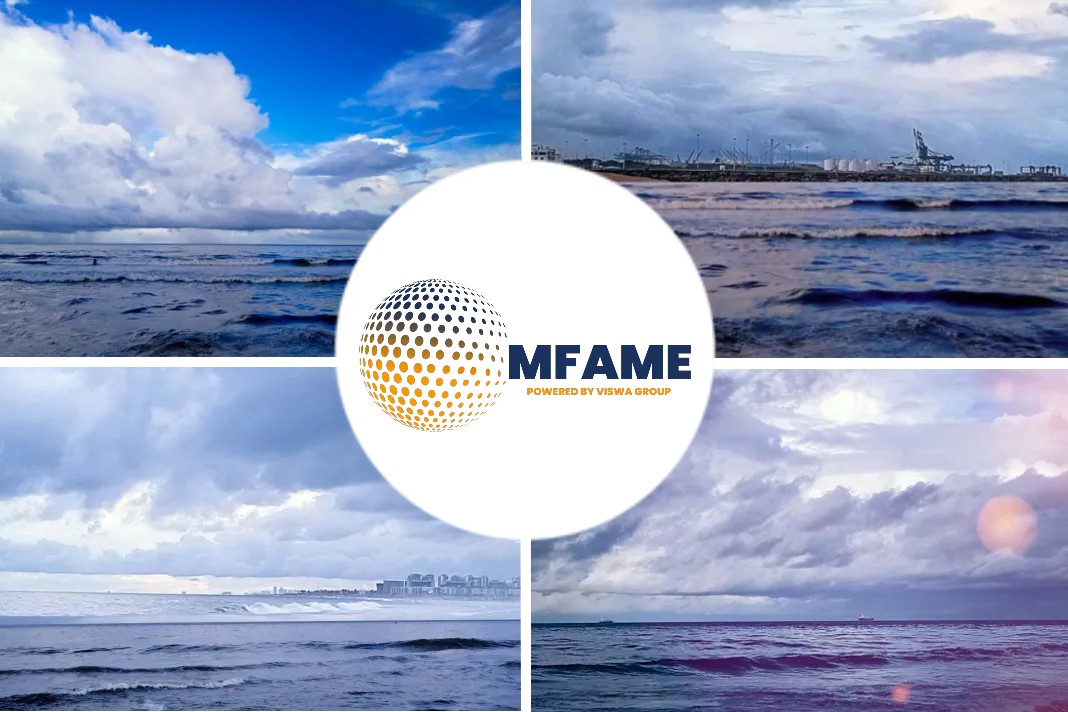
A recent news article published in the Live Bunkers speaks about What is Bunker (ship), About Bunker Fuel and Bunkering Procedure.
Bunker Definition
Bunker is term used for fuel used to power ships also known as marine fuel. The main types of fuels are FO380cst, FO180cst and MGO.
Bunker may be defined as the compartment which is placed generally on the side and / or bottom and it carries a ship’s fuel oil. It also refers to the fuel stored onboard. Bunker fuel may be defined as the low grade coal or heavy fuel which is used to power a ship. Bunker fuel is one of the derivatives of crude oil. In the simplest form, bunker fuel is the by-product left after the refineries have processed all the more valuable fuels from the crude.
Generally bunker fuel is very thick and heavy and it is required to be heated before using it in an Ship’s engine. Bunker fuel is comparatively difficult to store and transport. Basically bunker fuel is not readilly available like petrol and it is mainly stored at the major sea ports and it is sold and deilvered via contracts which are physical contracts to the marine vessels which are in need. Due to this factor the bunker prices vary widely from port to port. Generally bunker fuel is supplied by three means which are bunker barges, pipelines and road tankers. The way in which bunker fuel is supplied depends on the port and accessibility to the marine vessel. This material can be broken down in to different categories based on the chemical composition of the bunker fuels, intended purpose and the boiling temperature. As compared to the other petroleum products the bunker fuel is extremely crude and very highly polluting.
Inside the refinery
After the crude oil is extractracted from the under ground and brought to the refinery, the crude oils goes through a process which is known as fractional distillation. Fractional distillation is a process of separating a mixture of chemical compounds. Each part which is also known as fraction can be kept apart from the other chemicals. Different varieties of chemicals have different level of boiling points. Fractional distillation is mainly done by heating the mixture so as to get the evaporation of the fractions which are then condensed in their own compartments. Generally fractional distillation is accomplished in a distillation column, which siphoned off various fractions as they precipitated out. The oil refineries also used the catalysts to crack the hydrocarbon chains in the crude oil so as create specific oil fractions. Industrially, crude oil is heated and sent up along the fractionating column that has decreasing temperatures with height and several platforms at different levels to collect the condensate. Different components of crude oil have different boiling points. High molecular weight components have higher boiling points and condense at lower portions of the column while fractions with lower boiling points rise to the top of the column to condense. Smaller molecular components such as propane gas, naptha and jet fuel have relatively lower boiling points and they are removed at the initial stage of the fractional distillation process. The petrolem products such asdiesel and lubricating oil precipitate out more gradually more slowly and the bunker oil is present at the bottom of the barrel. The only thing that is denser than the bunker fuel is residue which is mixed with tar for the paving roads and the sealing roofs. Bunker fuels have very long hydrocarbon chains and as a result the bunker fuel is highly viscous. The bunker fuel is also very heavily contaminated with various substances which cannot be removed and this is the reason for very high pollution when the bunker fuels are burned. The thick fuel is difficult for most engines to burn since it must be heated before it will combust, so it tends to be used in large engines like those on board ships. Ships have enough space to heat this type of fuel before feeding it into their engines, and their extremely sophisticated engines are capable of burning a wide range of fuels, including low quality bunker fuel. As the bunker fuel also carries a range of contaminants, it can represent a serious environmental hazard when it spills.
Depending on the size of the ship and speed at which it is designed to cruise, the capacity & number of bunker are to be decided. Generally the capacities of bunker tank onboard ships are varying from 150 cubic meters to as big as 3500 cubic meters. One might wonder why the ship’s bunker tank capacity is big. The answer is that as the engine power increases, the fuel consumption also increases. Obviously the only practical way to deliver such large quantities of oil on board the ship from the barge is to use the arrangement of pipelines and pumps. There is a network of pipelines on the ship as well as the barge which are connected to the actual tanks deep below. The valves which control and regulate the flow of fluid to these pipelines are located on the deck at convenient places.
Bunkering Procedure
The generally applied bunkering procedure on a ship and important points that are to be taken into consideration while bunkering are described below
Before Bunkering
- The chief engineer on the ship is responsible for the calculation and to check which bunker / fuel oil tanks are supppose to be filled after he gets the confirmation from the shore office about the amount of fuel which is to be received.
- It might be required to empty some bunker tanks and transfer the bunkers from one tank to other. This is required so as to prevent mixing of two bunkers and prevent incompatibility between the previous bunker and the new bunker fuel.
- Generally a meeting should be held between the members that will take part in the bunkering process and they should be explained and have to monitor the following areas:
- Which bunker tanks are to be filled.
- Sequence order of tanks to be filled.
- How much bunker is to be taken.
- Emergency procedure in case oil spill occurs.
- Sounding is taken before bunkering and record is made.
- A checklist is to be filled so that nothing is missed on.
- All deck scuppers and save all trays are plugged.
- Overflow tank is checked to be empty.
- Adequate lighting at bunker and sounding position is to be provided.
- No smoking notice should be positioned.
- On board communication between the people involved in bunkering is made.
- Red flag/light is presented on masthead.
- Opposite side bunker manifold valves are closed and blanked properly.
- Vessel draught and trim is recorded before bunkering.
- All equipments in SOPEP (shipboard oil pollution emergency plan) locker are checked to be in place.
- When bunker barge is secured to the ship side, the persons involved on barge are also explained about the bunkering plan.
- Barge paperwork is checked for the oil’s grade and the density if they are as per the bunker specification.
- The pumping rate of bunker is agreed with the bunker barge.
- The hose is then connected to the manifold.
- All the valves required are open and checked.
- Proper communication between the bunker barge and the receiving ship is to be established.
- Sign and signals are to be followed as discussed in case of communication during emergency.
- After this, the manifold valve is open for bunkering.
During Bunkering
- During start of the bunker the pumping rate is kept low, this is done so as to check that the oil is coming to the bunker tank to which the valve is opened.
- After confirming the bunker fuel is coming to the proper tank the pumping rate is increased as agreed before.
- Generally only one tank filling is preferred because gauging of more than one tank at a time increases the chances of overflow.
- The max allowable to which tank is filled is 90 % and when the tank level reaches about to maximum level the barge is told to pump at low pumping rate so as to top up the tank, and then the valve of other tank is opened.
- During bunkering, sounding is taken regularly and the frequency of sounding is more when the tank is near to full. Many vessels have tank gauges which show tank level in control room but this is only to be relied if the system is working properly.
- The temperature of bunker is also to be checked; generally the barge or supplier will provide the bunker temperature. Temperature above this may lead to shortfall in bunker.
- A continuous sample is taken during bunkering with the help of sampling cock at the manifold.
After Bunkering
- Draught and trim of the ship is checked.
- Take sounding of all the tanks bunkered.
- The volume bunkered should be corrected for trim, heel and temperature correction.
- In general for each degree of increase in temperature the density should be reduced by 0.64 kg/m3.
- Four samples are taken during bunkering. One is kept onboard, one for barge, one for analysis, one for port state or IMO. One sample is given to barge.
- The chief engineer will sign the bunker receipt and the amount of bunker received.
- If there is any shortfall of bunker received the chief engineer can issue a note of protest against the barge/supplier.
- After everything is settled the hose connection is removed.
- The sample is sent for laboratory analysis.
- The new bunker should not be used until the report from the lab.
Did you subscribe to our Newsletter?
It’s Free! Click here to Subscribe.
Source: Live Bunkers