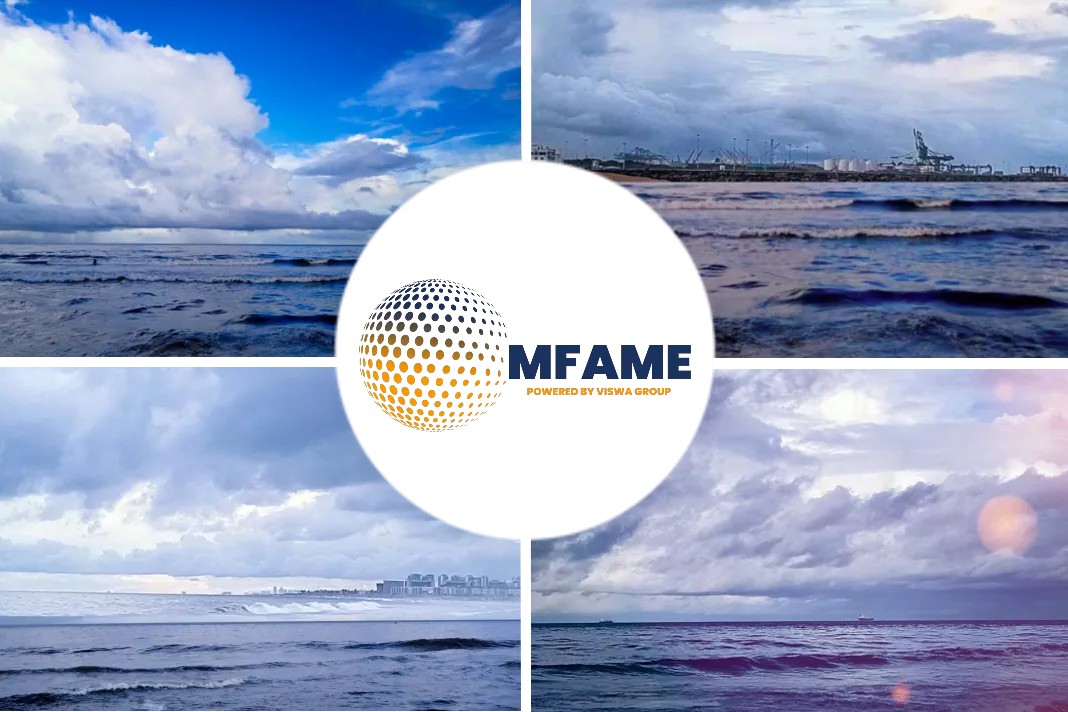
How do you handle container loading capacity issues or errors and prevent them from recurring? intrigues a LinkedIn post.
Container loading capacity
Resolve the issue or error
The next step is to resolve the issue or error as soon as possible before it causes further delays, damages, or losses. Depending on the nature and severity of the problem, you may need to adjust, reposition, or replace the container, or change the loading plan, equipment, or documentation. Communicate with the relevant parties, such as the shipper, the carrier, the terminal, or the customs, to inform them of the situation and coordinate the actions.
As a motor carrier it is our responsibility to report any and all issues to the shipper and to the roadability shop at origin before pick up. Rail yards and ship yards where carriers generally pick up intermodal containers all have roadability mechanics on site for repairs and adjustments and also for registration stickers and paperwork.
Analyze the root cause
The third step is to analyze the root cause of the issue or error and determine why it happened and how it can be prevented in the future. Collect and review the data, feedback, and records related to the issue or error, and identify any gaps, weaknesses, or risks in the processes, systems, or policies. Also make sure to consult with the experts, stakeholders, or partners involved in the container shipping, and seek their opinions and suggestions.
Implement corrective actions
The fourth step is to implement corrective actions to address the root cause of the issue or error and improve the container loading capacity management. This may include updating or revising the processes, systems, or policies, training or retraining the staff, upgrading or repairing the equipment, or enhancing quality control or monitoring. You should also document and communicate the changes and the expected outcomes to the relevant parties.
Monitor and evaluate the results
The fifth step is to monitor and evaluate the results of the corrective actions and measure their impact on the container loading capacity performance. Use indicators, such as loading time, utilization rate, accuracy rate, or error rate, to track and compare the results before and after the changes. Collect and analyze the feedback and data from the parties involved in the container shipping, and identify any issues or opportunities for further improvement.
Learn and share the lessons
The sixth step is to learn and share the lessons from the issue or error, and the corrective actions, and apply them to other container shipping operations. Document and disseminate the best practices, tips, or recommendations to the staff, partners, or customers involved in the container shipping, and encourage them to adopt them. Participate in forums, events, or networks related to container shipping, and exchange ideas and experiences with other professionals.
Did you subscribe to our daily Newsletter?
It’s Free! Click here to Subscribe
Source: LinkedIn