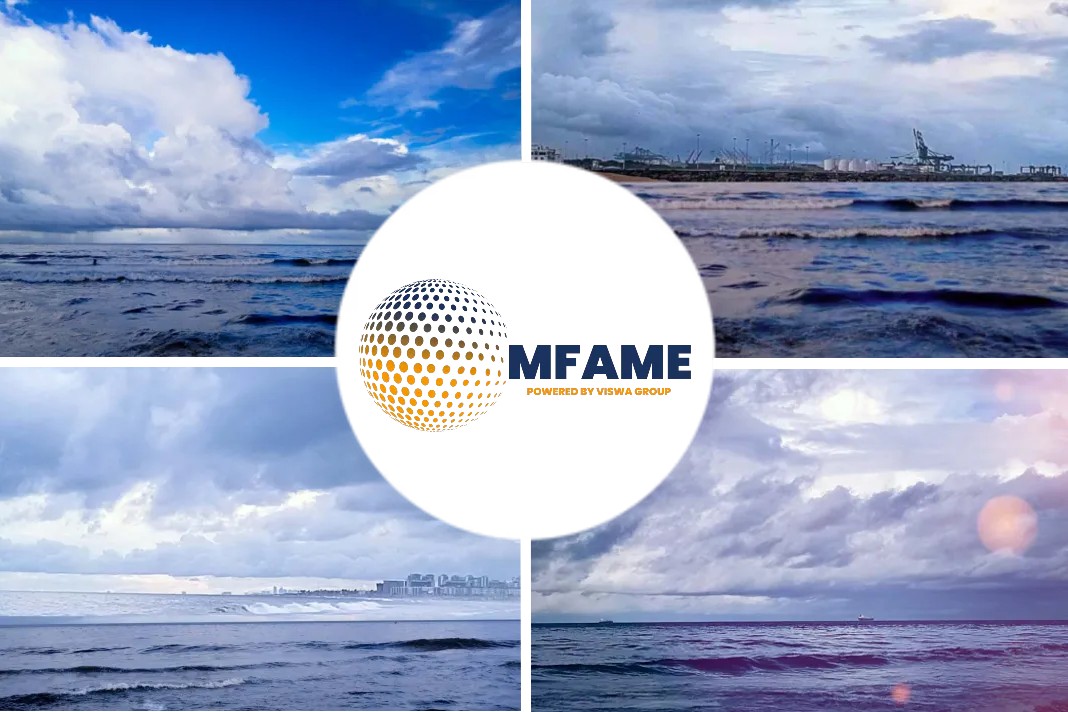
The function of any pump is to transfer liquid from one point to another and this involves the use of piping. Such a transfer in a tanker can be divided into two parts:-
- The movement of liquid from the tank to the pump. This is a function of the pump and its installation design. These factors are beyond the control of the ship provided the design ratings of the pump are maintained.
- The onward movement of the liquid from the pump to its destination. This is an area where the efficient operation of the pumps is essential if optimum results are to be obtained.
The major factors influencing pumping performance are discussed below. The flow of liquid to and from the pump must be matched exactly and this requires the flow on the suction side to be equal or greater than the discharge rate of the pump. Where the flow to the pump suction falls below the pumping rate cavitation will occur with the possibility of loss of suction and pump damage.
Centrifugal pumps do not suck liquids. The only factors which cause liquid to flow to the pump are:-
- Pressure acting on the surface of the liquid.
- The height of the liquid level in the tank in relation to the pump suction. Since no centrifugal pump can generate a total vacuum at its suction inlet, only a proportion of the atmospheric pressure can be usefully employed. Therefore, before a pump can operate satisfactorily, a certain pressure must exist at the pump suction and this is known as the required Nett Positive Suction Head.
Centrifugal Pumps
The centrifugal pump has for many years been the most suitable pump where a high pumping capacity is the most important factor. The size and cost of such a pump does not increase in proportion with the throughput, as it is not a positive displacement pump. It requires either the provision of ancillary self-priming equipment for the removal of air in the system or a separate stripping system.
In a centrifugal pump the motive force is provided by a rotating impeller which takes its suction at its centre and centrifuges the pumped liquid outwards to the casing discharge. The head generated is dependent on the diameter, blade angle and speed of rotation of the impeller. Flow rate is affected by the pressure in the discharge system and can fall to zero. Reverse flow through the pump can occur if a non-return valve is not fitted and operational on the discharge side of the pump.
The correct and efficient use of centrifugal pumps requires the observance of certain basic operating principles. Guidance on these principles is given here however, as manufacturers may incorporate special design features to meet operational requirements, the information given here must be read in conjunction with the manufacturers operating instructions and on board procedures organised. The basic characteristics of a centrifugal pump are:-
- Throughput varies with speed.
- Head varies as speed squared.
- Power required varies as speed cubed.
These relationships are subject to appreciable variation caused by the system in which the pump operates.
Positive Displacement Pump
Unlike the centrifugal pump, the positive displacement pumps used in dedicated stripping systems are capable of a low suction pressure and the ability to pick-up suction without external priming. This type of pump includes steam reciprocating pumps and ‘screw’ type pumps. Both types are now mainly used for stripping tanks or as specialised cargo pumps.
The suction and discharge valves of a positive displacement pump must always be open before starting the pump and must remain open until the pump is stopped. These pumps must not be operated in excess of their design speed and particular care must be taken to avoid these pumps over-speeding when they lose suction. Pressure relief devices must be checked at regular intervals to ensure their correct operation.
Submerged Pumps
Submerged pumps are relatively common on chemical carriers. This type of pump is usually powered hydraulically or electrically and provides for a pump located in each tank. Manufacturer’s instructions must be complied with for efficient operation of these pumps.
Submersible pumps are purged, using inert gas (ship’s IG or nitrogen) or air, as a means of checking for seal condition and tightness. The pumps must be purged before and after every loading/discharging/tank cleaning operation and the appropriate record form completed.
If the purging records indicate a deviation from the manufacturer’s recommended parameters, such as pump cofferdam is blocked or excessive seal leakage being detected, the management office is to be notified and appropriate corrective action is to be taken at the first opportunity.
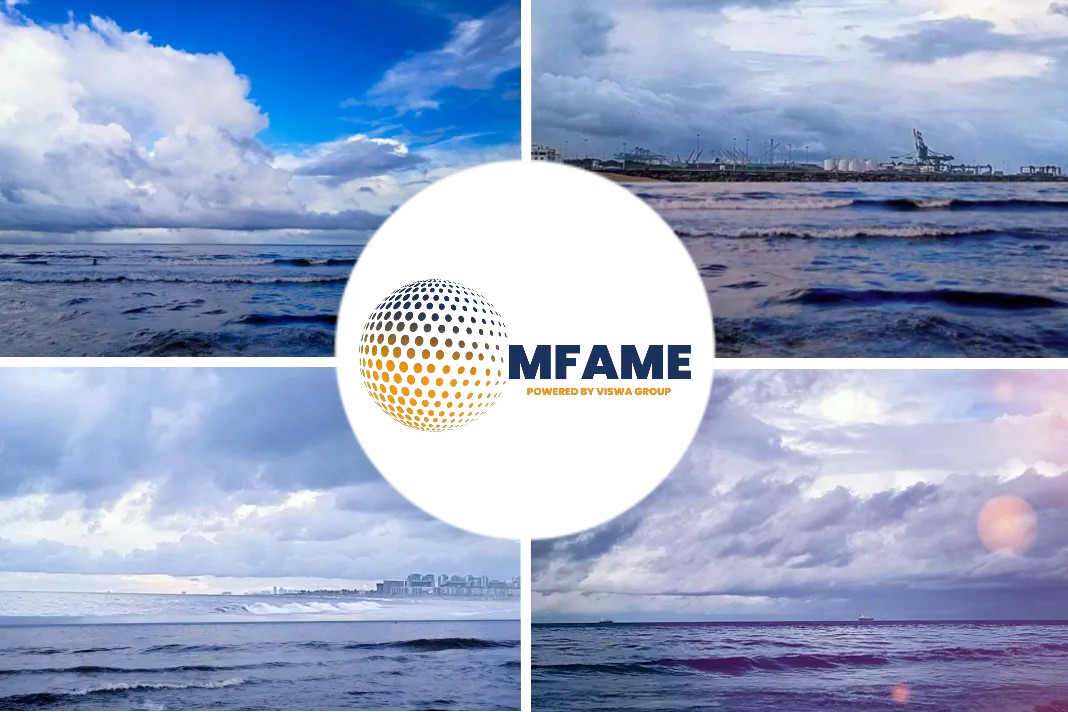
Portable Submersible (Emergency) Pump
Portable submersible pumps, are provided on chemical ships and other specialised liquid cargo carriers, for discharging cargo in the event of a main cargo pump failure. The pumps are usually hydraulically driven and lowered directly into the tank generally through a tank cleaning hatch.
All necessary safety precautions relevant to the actual cargo being handled are to be observed and permission obtained from the local port authorities before operations are commenced. It is a good practice to shutdown the hydraulic oil pressure system before connecting and disconnecting hydraulic hoses of portable hydraulic driven emergency pumps.
Use of eductors
Eductors may be used for ballast stripping purposes. To strip efficiently, an eductor used for tank cleaning operations should have a capacity of about twice the rate of liquid being introduced to the tanks.
- Eductors are always to be operated at or near their design driving pressure as, in general, lower driving pressures will considerably reduce eductor efficiency. Higher back pressures in the system than the eductor was designed for can also reduce suction capacity.
- The eductor drive liquid must always be flowing before the suction valve is opened to prevent back flow of the driving liquid to the tank suction.
- When shutting down an eductor the suction valve is to remain open until the eductor is stopped to prevent the eductor drawing a vacuum on the suction line.
- If, during use, the eductor driving pressure falls below the required operating pressure, the eductor suction valve is to be closed to prevent backflow of the driving liquid. The tank suction must not be used to prevent backflow as the suction pipework is not designed for such high operating pressures.
Recommendations
High melting point cargoes such as Phenol, Palm fatty acid distillates lauric and Stearic acid has inherent property to form lumps of cargo. It is therefore recommended to turn the cargo pumps at regular intervals during the voyage and prior to discharge in order to avoid any last minute surprises. All the lines to be then blown back to the cargo tanks.
The danger of frozen valves, pressure/vacuum in the tanks to be monitored during loading, voyage and discharge. In the event if any of the pumps are found frozen, deployment of portable Framo pump should not be considered without a proper risk assessment and office permission.
Did you subscribe to our daily Newsletter?
It’s Free! Click here to Subscribe
Source: Chemical Tanker Guide