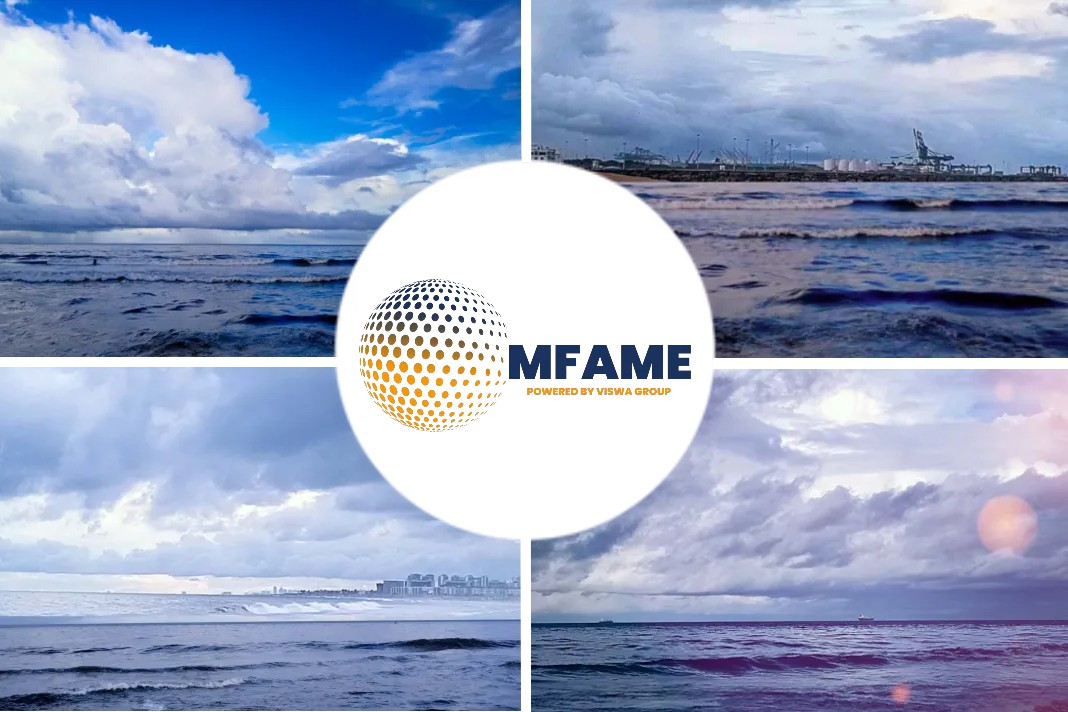
IMCA safety flash reports of a person struck in rigging accident.
What happened?
During the loading of subsea hatch covers onto a vessel, a member of the rigging crew was struck and badly injured by a 55 Te shackle connected to a steel wire sling and fibre lifting sling, which formed part of the lifting arrangement used to lift the covers.
The hatch cover was safely landed on deck. However, during the lowering of the lift rigging to enable the crane to be disconnected, a slack leg of the lifting bridle, which would only come into use during deployment subsea, came to rest on the top flat section of the hatch cover. Instructions were given by the banksman to ‘stand by’ whilst the crane manoeuvred to free and lower the slings to deck. The volume on the injured person’s radio had previously been turned down due to feedback from other users’ radios, and subsequently he missed the safety command from the banksman. The rigger approached the load and within 5 seconds of doing so the rigging suddenly fell from the top of the cover and struck him. The rigger sustained multiple injuries including a fractured and dislocated right clavicle, fractured spine in several places, broken ribs and bruising to the lung.
What was the cause?
IMCA member drew the following conclusions:
- The design of the cover allowed objects to come to rest on top.
- The rigging design was overly conservative and too big and heavy for the job in hand.
- Misleading rigging drawing did not show slack sling.
- There was a breakdown in verbal communication (radio interference, terminology, understanding).
- The rigger acted without thinking deeply – “fast thinking” and entered the line of fire.
- There were missed opportunities to use existing safety mechanisms (such as the toolbox talk, task risk assessment, the stop work authority, the management of change process).
Key Learnings identified
See things from a different perspective: keep in mind during the engineering design phase how the crew will be affected by design choices and try to eliminate or mitigate undesirable effects before equipment reaches the worksite.
“Fast thinking” in response to a developing situation or to personal biases such as self-pressure, pride, desire to please others or pre-empting an outcome, can lead us unwittingly into the line of fire. This is natural behaviour and not an intentional violation, but by being more aware of our own and other biases and responses we can better manage them.
Communication breakdown plays a part in almost every incident.
- Technology such as bone conduction headsets can help us minimise disruption due to feedback and surrounding noise whilst allowing the wearer to maintain situational awareness.
- Standardised communications protocols such as challenge and response, and repeat back, can help provide positive assurance that a message has been received and understood as intended.
- Drawings are a form of communication and should provide information to end users without misleading them.
Work as imagined versus work as done: How people writing procedures imagine the job is done can be quite different from reality at the worksite. Where practicable, we need to include the end user in the development of procedures. Failure to follow a procedure step by step on every single occasion, is not a wilful violation or a root cause when something goes wrong.
Did you subscribe to our daily newsletter?
It’s Free! Click here to Subscribe!
Source: IMCA
Wow, awesome weblog layout! How long have you ever been running a blog for?
you make blogging look easy. The entire glance of your site is wonderful, let alone the content material!
You can see similar here sklep internetowy