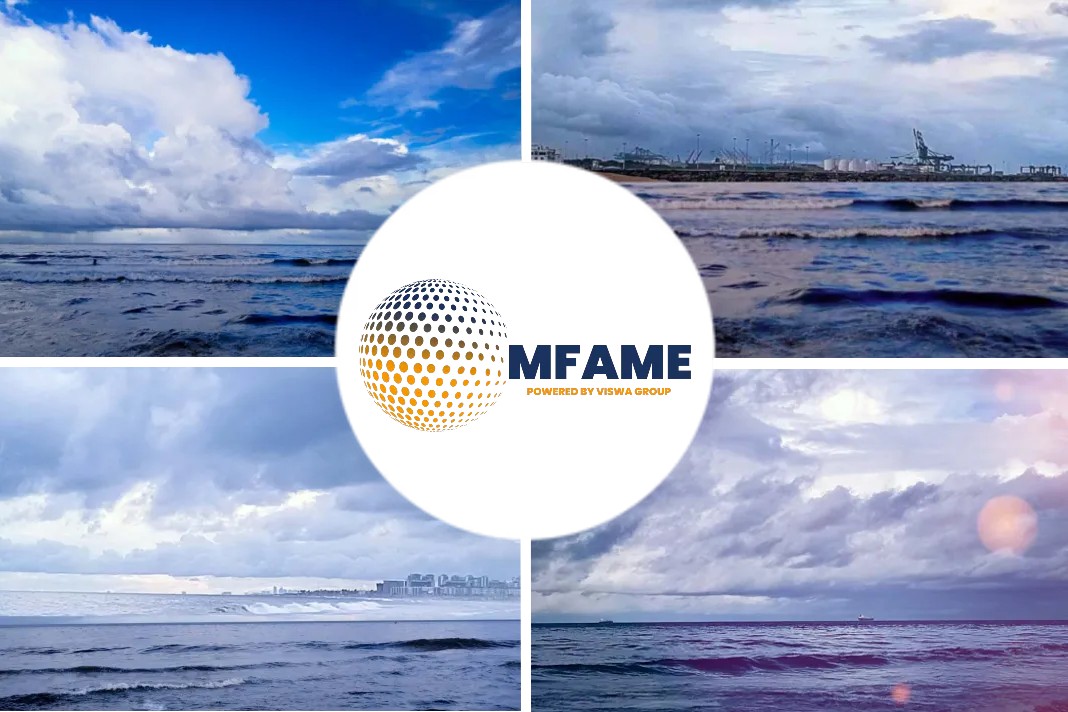
Generally, there are two compressors onboard a ship ( can be more than two depending upon the requirement of the vessel.) The two compressors fill up the air receivers, which should have total capacity such that the engine can start 12 times ahead and astern without replenishment of the receivers. This capacity is limited to 6 times if it’s a unidirectional engine, reports Marine Insight.
Air compressors
Each of the air receivers is fitted with a relief valve, which will limit the pressure rise to 10% of the maximum design pressure of the receiver.
Also, the outlet of the relief valves should be outside the engine room so that it doesn’t contribute in case there is a fire near the air receiver.
Usually, air compressors onboard are capable enough to charge both the air receivers from zero to full in one hour.
The air compressors are fitted with several safety devices as well such as relief valves on each stage which limit the pressure rise to 10% of the maximum working pressure.
The delivery side is fitted with a high-temperature switch which cuts off the compressor at a specified temperature or a fusible plug which may melt at 121 degrees centigrade.
Performance of the marine air compressor is taken at the end of every month to ascertain the working capacity of the compressor.
The performance report includes the delivery air temperature, cooling water inlet and outlet temperatures, lube oil pressure and discharge pressures of each stage of the compressor.
The compressor is generally started in an unloaded condition so that minimum current is drawn by the motor and the bearings are devoid of oil.
Maintenance jobs carried out on the main air compressor depending on the running hours of the compressor and all these jobs are mentioned in the maintenance manual of the compressor.
- The planned maintenance system devised by the company must be strictly followed else there can be a severe breakdown
- To avoid breakdowns in the main air compressor, the following maintenance must be considered
- Daily morning and evening rounds including checking of lube oil level, discharge pressures of various stages, discharge temperature and running time of the compressor.
- When an engineer takes over, he/she must first take note of all the maintenance jobs that might be due in his/her contract, and take spare part inventory and order the spares, if required with the help of Chief Engineer.
- The engineer must also note the torques required for tightening various bolts, screws and nuts on the main air compressor.
- The testing of air compressor alarms must be carried out as per the PMS, which generally demands the alarms to be tested once every three months.
- One of the most important things in the main air compressor is the bumping clearance of the compressor, which will be discussed later in the compressor maintenance.
- As a basic thumb rule, the main air compressor should run for 3-4 hours every day on an MR tanker. If the running hours exceed this duration, then the required checks must be carried out.