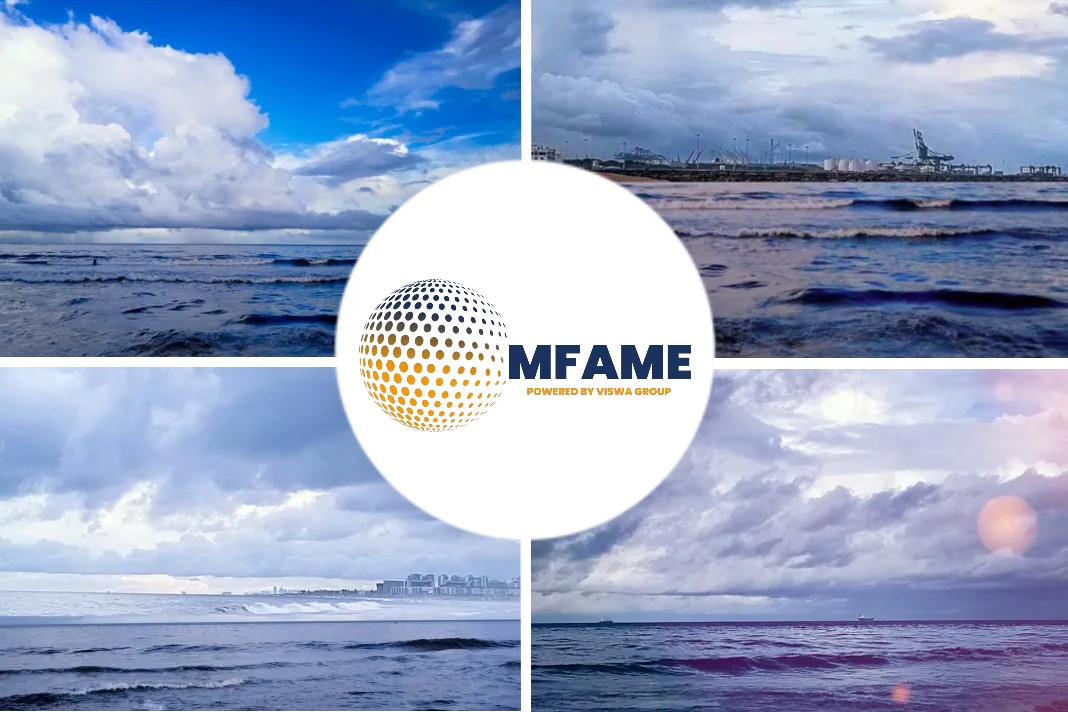
Guidance on how to comply with PSC focus on firefighting and clean machinery spaces, mentions an IIMS news source.
Liberian Administration’s guidance
The Liberian Administration has released guidance on how to comply with the recent focused trend of inspection of machinery spaces by various Port State Control (PSC) regimes.
There has been an increased focus on the proper operation of firefighting equipment and cleanliness of machinery spaces. Specifically, the following items are consistently noted by Port State Control Officers:
– Engine room water mist system set in “Manual” mode.
– Fuel oil quick closing valves blocked open by use of wedges or wires.
– Pipe insulation laggings wrongly installed, sometimes soaked in fuel oil or missing.
– Excessive fuel, oil accumulation and lubrication oil leaks in machinery spaces, auxiliary engines, steering gear room or purifier room.
– Inoperable fixed gas detection systems, missing ships procedures on how to test the system, lack of crew knowledge on the proper operation of fixed gas detection systems, ships lacking the appropriate span gas to test the system or not having any span gas available, and missing specific testing equipment (adapter to connect to the sample point, appropriate regulator to hook up to the span gas, inflatable bags to hold the gas).
Engine room water mist systems
Engine room water mist systems must be readily available for immediate use and in good working order. Activation switch on the system control panel must be set on “Remote” or “Automatic.”
Precaution shall be taken to prevent the nozzles from becoming clogged by impurity in the water, regular checks must be carried out to identify corrosion of piping, nozzles, valves and pump.
Quick closing valves
Quick closing valves are positive shut off valves that are designed to isolate oil tanks in the event of a fire and also prevent fueling of a fire in circumstances where system piping and components are compromised.
Such valves must always be free to operate, manual wires activators and/or hydraulic systems must be kept under close examination and tested regularly. Under no circumstance shall a valves operation be hindered by fitting wedges or wires to preclude the activation.
A maintenance plan should be in place, including technical manuals containing diagrams and information that describe the system components, required spare parts, operation, maintenance and repair.
All engine department personnel should be able to identify the location of each valve, the respective remote closure and how to close them locally and remotely in an emergency.
Insulation lagging
Insulation lagging should be inspected regularly. Inspection should include looking for signs of cracking, distortion or any damage or signs of a hot spot. Evidence of leaks shall be acted upon with celerity and corrected to prevent possibility of fire.
Equipment hot spot should be identified and insulated in order to prevent the creation of areas that could ignite a fire in case of sprays or leaks in the system.
Fuel and Lubricant
Fuel and lubricant leaks can easily lead to a fire or an explosion due to their highly flammable nature or create pollution and hazardous situations. Leaks from fuel pumps, main engines, generators and steering gears shall be corrected immediately.
The administration notes that adhering to a robust preventative maintenance system ensures that repairs are carried out prior to the development of leaks that can lead to fires, pollution and are a common reason for ships to be detained by port state control. Following areas have been known for leaks and oil accumulation:
– In vicinity of double jackets pipes on top of main engine
– Accumulation on top of main engine
– Oil leaks dripping down the main engine crack case
– Bilge area around the lube oil pumps behind the main engine
– Under the rocker covers of auxiliary engines
– Fuel filters for the auxiliary engine
– Underneath the auxiliary engine platforms
– Underneath the lube oil/fuel oil purifiers
– Oil soaked lagging in purifier room
– Shaft penetrations of any fuel/oil pumps
– Valves throughout any fuel/oil piping
– Oil soaked lagging throughout any fuel/oil piping
– Sides/bulkheads of tanks in the engine room
Did you subscribe to our daily Newsletter?
It’s Free! Click here to Subscribe!
Source: IIMS