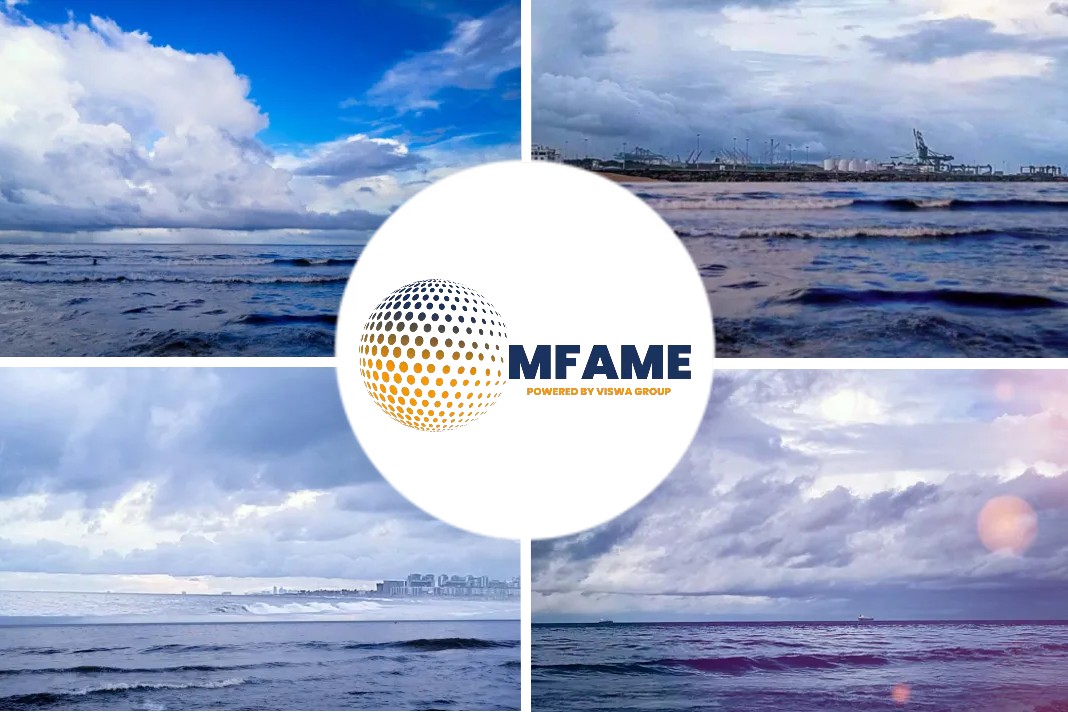
- Resistance increases fuel consumption and CO2 emissions as the engine needs to work harder to move the car along.
- Cleaning may be needed to remove any accumulated fouling and return the vessel back to optimal performance levels.
- One carbon credit is issued for every tonne of CO2 avoided using more energy-efficient biocide-free coatings.
In 2023, the attention of shipowners and charterers alike will turn towards the changes to legislation aimed to tackle greenhouse gas emissions. Maintaining and monitoring a well-coated hull could be a low hanging fruit.
Reducing CO2 emissions
The recent amendments to MARPOL Annex VI have brought the introduction of the carbon intensity indicator (CII) and CII rating and the Energy Efficiency Existing Ship Index (EEXI), prompting questions on how coatings can be of influence.
But how can the hull coating of a vessel have a positive or negative impact on the CII rating? There are many similarities between a CII rating and fuel consumption of a car.
If you drive a car with flat tyres, windows, doors, and sunroof open you’ll create extra resistance. Resistance increases fuel consumption and CO2 emissions as the engine needs to work harder to move the car along.
Clean hull coating
CO2 emissions from a ship’s engine also increase with fuel consumption. A vessel with a fouled hull or rough hull coating will use more fuel and create more emissions than the same vessel with a smooth coating.
A vessel’s CII rating is proportional to the fuel consumed and emissions created, therefore, an improved CII rating can be gained by reducing hull fouling.
To learn more about how coatings can impact ship-generated emissions, we spoke to Chris Birkert of marine coating specialists Akzo Nobel.
Coating’s role influencing EEXI and CII
There is some confusion in the market about EEXI, and we see different approaches from class societies on this topic.
Most class societies do not consider coatings impacting upon EEXI and require in-service speed trials for proof of improvement.
DNV are taking a different approach and have a methodology to account for changes in hull roughness and therefore the EEXI rating.
We have received increasing enquiries on CII ratings. We can provide CII rating predictions by combining our vessel performance prediction tool, Intertrac® Vision, with our newly developed CII calculator.
This accounts for several parameters including the operational profile of the vessel, the coating selected and the substrate preparation.
This supports shipowners in their choice of fouling control system for the underwater hull. Now, almost all drydocking discussions include a predictive analysis of CII rating.
Owners are also asking about the synergies between coatings and other energy saving technologies, as well as performance predictions between coating technology ‘A’ versus coating technology ‘B’ as they plan for the vessel’s next drydocking.
Anchoring in warmer climates impact fouling
Water temperature is only one of many influences. UV levels, pollution, nutrient levels, seasonality, and lunar cycles also impact the fouling loading that the underwater hull will face when static.
Our Intertrac® system maps all these parameters and can provide advice to shipowners on the optimal location to lay-up.
The coating technology type applied to the immersed areas of the underwater hull will also determine how long the vessel can remain there without needing inspection and cleaning.
Cleaning may be needed to remove any accumulated fouling and return the vessel back to optimal performance levels.
Biocidal products must deliver biocides at a higher rate than the bio-challenge, which can be plant (weed, grass, or algae) or animal based (barnacles, molluscs, tubeworms, sea squirts), otherwise the organisms are not controlled and will begin to grow.
Foul release systems provide ‘non-stick’ surfaces which organisms find it difficult to strongly adhere to and are easily removed by waterflow or light cleaning.
Self-polishing co-polymer biocidal anti-fouling and foul release coatings remain the go-to type of products for optimal performance in these high challenge areas, where fouling organisms are numerous and grow quickly if ships hulls are not protected.
Fouling control coating products
Our in-house performance prediction tools show good correlation to in-service performance as measured on board the vessel.
However, only a small percentage of vessels have onboard performance monitoring systems installed, something we think is essential when faced with increased scrutiny on emissions reporting.
Analysis of the publicly available vessel emissions data shows clear performance differentiation between vessels which have applied what we would consider to be ‘high-end’ fouling control coating products, such as biocidal self-polishing copolymer antifouling coatings and premium foul release coatings.
Increasing docking cycles over five years
Due to extraordinary freight rates in the market, we have seen several customers requesting class approval for drydocking extensions, especially within the container sector.
This does cause issues where the vessel has been coated with a polishing scheme which may be stretched beyond its specified lifespan.
Whether this prompts shipowners to apply 90-month schemes as standard at future drydocking remains to be seen for biocidal polishing type systems.
Our 10-year coating offer combines our foul release Intersleek product with our Intertrac® HullCare hull management service.
This provides an option to extend docking intervals to 10 years with an intermittent 5 year in-water survey if class allows, or a much shorter drydocking where only minor repairs of the hull coating are required.
Generating carbon credits through hull coatings
When changing the hull coating from biocidal to biocide-free foul release technology, owners can generate carbon credits with the voluntary carbon offsetting scheme Gold Standard.
One carbon credit is issued for every tonne of CO2 avoided using more energy-efficient biocide-free coatings.
Did you subscribe to our Newsletter?
It’s Free! Click here to Subscribe.
Source: Nepia