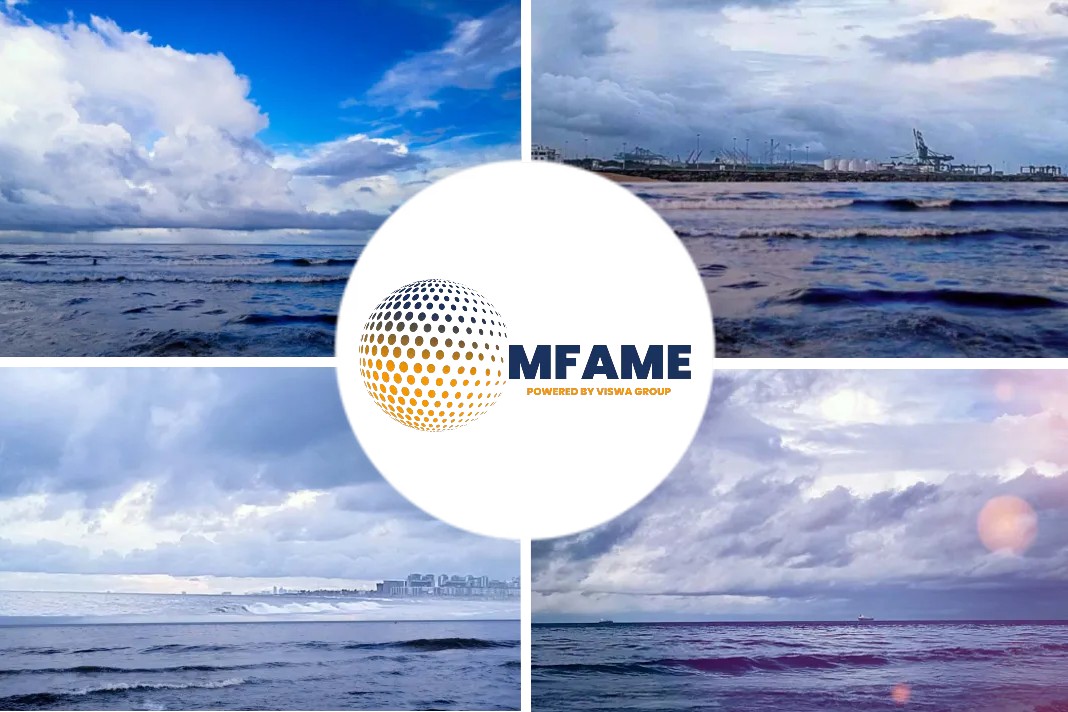
Taking proper samples of liquid cargoes is vital to protect shipowners’ interests when allegations of cargo contamination arise. Gard gives an overview of how and when to do it.
Disputes relating to “off-spec” or contaminated liquid cargoes are a recurring problem. Gard is often involved in cases where the shipowner has no independent evidence as to the cause of an alleged cargo contamination. The source of the problem could be in the shore tank at the load port, in the shore pipeline during loading or on board the vessel itself. The cargo could even have been manufactured out of specification prior to delivery to the terminal for shipment.However, if the cargo is found to be “off-spec” when the vessel arrives at the discharge port, and there is no evidence of contamination from the load port, the vessel could be faced with a potentially large claim even if the vessel is not at fault.
How and when to take samples
- Cargo samples should preferably be drawn jointly in the presence of a representative of the shipper, receiver, and terminal.
- Sampling equipment, including fixed fittings, e.g. sampling cock on the pipeline, must be thoroughly cleaned before use.
- Manifold and first foot samples should immediately be checked visually for any foreign particles, water and colour. If there is any suspicion that the sample may be off-specification, the terminal should be advised accordingly and loading operations should be stopped for further investigation.
- Sampling at loading, discharge and joint sampling should always be taken by an experienced crew member and/or surveyor.
- For more detail, see Gard Guidance to Masters 2.12.3.5.
Sampling at loading
- The most important sample is the ‘manifold’ sample taken at the vessel’s manifold at the start of loading, preferably with the manifold valve in a closed position. Loading should not commence until the manifold sample is approved.
- ‘First-foot’ sample: Taken from the tank when the cargo depth is approximately one foot deep. This is particularly important when loading sensitive and/or expensive cargoes.
- Samples taken from the manifold throughout the loading process, including after scheduled stoppages.
- Final tank samples, after completion of loading. These should be taken from multiple depths (low, middle, top) in case the cargo is not homogenous.
Joint sampling
- Ship’s crew should be wary of samples given to them by another party.
- The samples should be listed as ‘joint samples’ only if they were, in fact, taken in the presence of both ship’s crew and cargo surveyors.
- Ship’s crew should always take the same type of samples as the cargo surveyor onboard and retain these samples.
- Ship’s crew should always take their own manifold and final tank samples, whether or not the cargo surveyor also takes these.
Sampling at discharge
- Tank samples should be taken prior to commencement of discharge.
- Manifold samples should be taken at the vessel’s manifold at the start of discharge.
- The crew should take and retain the same samples as the cargo surveyor.
Case Study – the “Million dollar sample”
A chemical tanker was scheduled to load a parcel of refined glycerin from two different ports in Asia. The first parcel was loaded uneventfully, and the crew had taken all proper samples. In the second port, however, halfway through loading, the flow was stopped and the vessel was asked to vacate the berth. This is a worrying development.
The Master reported this to the head office, who in turn contacted Gard, their P&I insurer. The vessel had no choice but to follow instructions and vacate the berth. Since this was an unscheduled event, the crew drew a full set of composite samples of the cargo that had been loaded so far.
The vessel then re-berthed and resumed loading. The crew drew 5-6 new manifold samples, taken against a closed valve. They also took samples periodically throughout the loading. These were in apparent good order and condition. After loading was completed, the crew drew final tank samples, labeled them properly, and logged them in the cargo book.
When the vessel arrived at the USA discharge port, the entire cargo was rejected due to its odour. The receivers claimed it was unusable and demanded USD 2 million in security. As a result, the cargo had to be returned to the load port for reconditioning and the entire exercise proved very costly.
The good news was that since the crew had taken a large number of manifold samples from the second loading port, the shipowner was able to complete thorough testing of the cargo and could identify the contaminant which did not originate onboard. Eventually, all parties agreed to carry out a joint odour testing of the manifold samples. Once the sample bottle drawn by vessel crew was opened, it was quickly determined that the odour originated from the shore tank samples – meaning that the vessel and owners could not be held liable.
This goes to show how important – and cost-saving- proper cargo sampling can be. Because of the diligent work by the crew a large claim was avoided, and the ship was not held liable.
Key learnings
- When a contamination claim is made against a shipowner, proper sampling is vital to proving whether the contamination occurred onboard, or elsewhere in the supply chain.
- The most important sample is the ‘manifold’ sample taken before the start of loading. Without this sample, it is not possible to determine the condition of the cargo before it reaches the vessel cargo lines and tanks. Crew should not open the manifold valve and allow cargo to flow into the vessel cargo lines before the manifold sample has been approved.
- The crew should always take their own manifold and final tank samples, irrespective of whether cargo surveyors also take samples. Having your own set of ‘evidence’ is vital.
Did you subscribe to our daily newsletter?
It’s Free! Click here to Subscribe!
Source: Gard