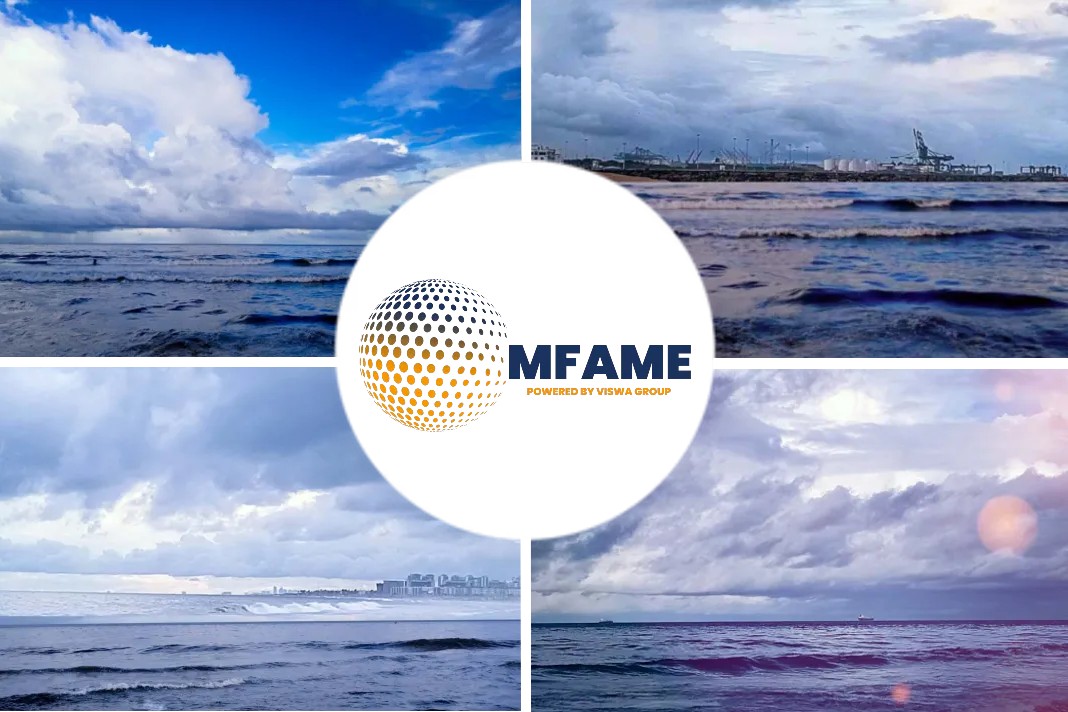
The Triple-E class container ships were built by South Korea’s Daewoo Shipbuilding & Marine Engineering (DSME), reports Ship Technology.
They are the largest container ships in the world, with a container carrying capacity of 18,000 twenty-foot equivalent units (TEU). Each vessel is estimated to cost $190m.
Triple-E (EEE) stands for economy of scale, energy-efficient and environmentally improved vessel. The vessels operate in the Europe-Asia route, with stops at Shanghai, Ning-bo, Xiamen, Yantian and Hong Kong ports.
Maersk Line signed a $1.9bn contract with DSME in February 2011 to build ten Triple-E class vessels. The deal included two options for ten additional vessels each.
The total value of the contract, including the option, is $5.7bn. It is considered as the single largest contract value in the shipbuilding industry.
The option for ten more vessels was exercised in June 2011. The first ten vessels were delivered in 2013 and 2014, and the second set of ten vessels was delivered in 2014 and 2015. The first vessel was delivered in July 2013.
Maersk piloted the use of up to 20% sustainable second–generation biofuels on a Triple-E vessel between March and June 2019. The trial was part of an initiative of Maersk and its partners to decarbonise ocean shipping.
Triple-E class container ship design
The Triple-E class is an improved and modified version of Emma Maersk, one of the largest active vessels in the world. Emma Maersk can carry 15,500TEU.
The improved vessel has a U-shaped hull so more containers can be accommodated at lower levels. Unlike Emma Maersk’s 22 rows across its width, the Triple-E vessels have 23 rows, accommodating an additional 1,500 containers.
The 165,000t vessel has a length of 400m. The beam is 59m and draught is 15.5m. The height above baseline is 73m, one metre higher than the highest ship Allure of the Seas. The new ships are designed to cruise at a top speed of 23k.
The navigation bridge and accommodation areas were relocated to five bays forward. The engine room and chimney were moved six bays back. These modifications create space for 1,000 extra containers. In all, the new vessels carry 2,500 more containers compared to Emma Mærsk.
The vessels are also the most energy efficient. They have the lowest carbon dioxide (CO₂) footprint by emitting 20% less CO₂ per container shipped when compared to the most efficient container vessel available currently. Optimised design allows the vessel to cruise with the maximum possible load at speeds prevailing in the industry.
The waste heat recovery system captures the exhaust gas from the engine and uses it to run the turbine to produce mechanical energy, which in turn, is used to run a generator. It cuts fuel consumption and CO₂ emissions by approximately 9%. The cost of installing a waste heat recovery system on each Triple-E vessel is approximately $10m.
Propulsion and engine power of Triple-E Class Container Ship
The Triple-E class vessel has a twin skeg propulsion system, with two slow running ultra-long stroke engines. Each engine drives a separate propeller.
Each engine produces 43,000hp and weighs 910t. Each consumes 168g bunker oil per kWH produced. Each of the two propellers has a diameter of 9.8m and four blades. The smaller the number of blades, the lower the resistance, while the larger diameter propellers produce more pushing power.
The two engines and two propellers combination generate further savings of four percent energy when compared to a combination of one engine and one propeller.
The Triple-E Class container ships are fitted with two shaft generator motors (SGM) with a rated capacity of 3MW each. The motors act as variable power generation units.
Suppliers involved
Mecklenburger Metallguss supplied the propellers and Siemens provided the SGM and power generation systems which were enabled by Waste Heat Recovery System (WHR).
Siemens also equipped the vessel with its EcoMain Decision Support System.
GEA Westfalia Separator Group supplied 160 eagle-class separators for the vessels. Danfoss Semco supplied its patented VTL Drives frequency converters installed in the engine room.
KRAL delivered 600 screw pumps, which act as transfer, supply and circulation pumps for the booster modules.
Did you subscribe to our Newsletter?
It’s Free! Click here to Subscribe!
Source: Ship Technology