A recent news article published in the Ships Business highlights on the Use of inert gas system in tanker operation.
What is Inert Gas?
What is Inert Gas? It is a noble gas that does not undergo a chemical reaction with any substances. This non-active characteristic of inert Gas makes it the perfect medium to prevent cargo explosion on vessels.
Vessels carrying cargos that produce hydrocarbon vapors require an inerting solution to eliminate the risk of explosions and fires in cargo tanks ( crude oil tankers, chemical tankers, product tankers, gas carrier, etc.). Inert Gas System is used to keep the oxygen content below 8%, a standard set by the International Maritime Organisation ( IMO ). The system offers a combustion solution that creates inert Gas out of the burning process that contains less than 8% oxygen and a non-explosive atmosphere in the cargo tanks. Fire needs oxygen, heat, and fuel to burn. Removing one of the elements in this fire triangle will prevent fire. The fundamental aspect of introducing inert Gas to any compartment that contains a mixture of hydrocarbon gases is to remove the oxygen content. The system, therefore, minimizes the risk of explosion.
Inert Gas (IG) piping Fitted on all tankers over 20,000 dwt and all tankers fitted with crude oil washing (COW) systems. IG piping is usually large diameter low-pressure mild steel, with smaller diameter branch lines. The internal surface of inert gas piping does not usually corrode. The external surface is painted but will corrode if the paint coating deteriorates. Using the inert gas system on board tankers required some careful consideration.
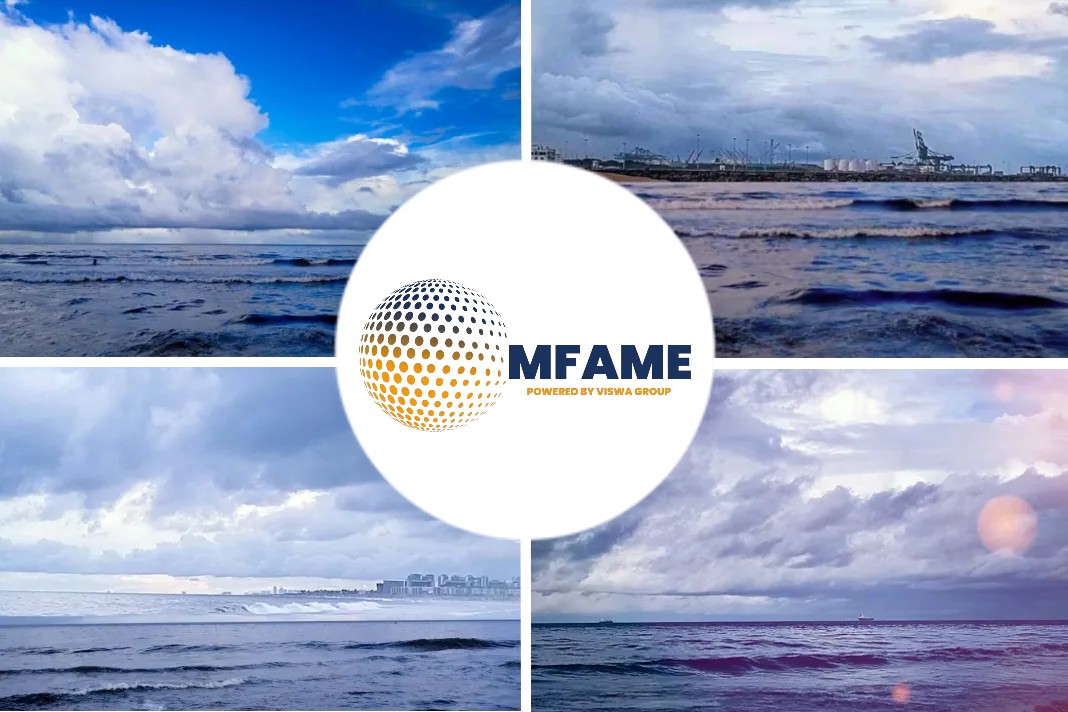
Below guideline should be followed when operating the inert gas system
During Operation Of Inert Gas System (IGS)
The oxygen content of the Inert Gas (also called IG) supplied to cargo tanks should be 5% or less. However, it is to be noted that too little content of oxygen in the IG would introduce other impurities into the cargo tanks. During the operation of the Inert Gas system (IGS), the automatic Recorder for Oxygen (O2) and IG Pressure on the mainline must be operational. The details of the start of operation (such as discharge at XXX port, date and time of mark, etc. should be noted on the recording) Before the start of the IGS, ensure safety confirmation as per the Operational Record. The inspection of the deck seal and PV breaker must be confirmed in good condition. Also, the status of the alarm, indication, and proper operation and sequence of related equipment must be observed.
Prior arrival discharge port, follow the company’s designated Tanker Discharging Checklist for IGS preparation and checks/tests. For the operation of the IGS and precautions, refer to IGS operation makers manual, which is provided to each vessel. Starting in Inert Gas System before entering discharge ports of environmentally sensitive nature, where the air pollution and scrubber discharge flushing could interfere with the ecosystem, the Inert Gas System should be run before embarking the harbor pilot at the time of entering the port. It is done so that the IGS plant can settle down & avoid dark funnel smoke emissions on start-up.
Cargo Discharging Operations
Operate and test the IGS before arrival at the discharge port. Ensure that O2 level in all cargo oil tanks is less than 8% (preferably less than 5%) using Double Hull (D/H) Operational Record – Voyage record of COT Oxygen / H2S content. Also, the cargo tank pressure shall be reduced to minimum positive IG Pressure (pressure minimum 100 mmAq.) Before starting of Discharge Operations, re-confirm all cargo Tank openings are tightly closed (e.g., Vapor locks used for tank gauging, etc.). Cargo tank IG supply valves should be correctly set, before starting IG on deck (i.e., opening IG main supply valve). The individual Cargo Tank IG valve key is to be kept within the control of the Chief Officer.
Monitor the cargo oil tank O2 level, Pressure parameters, and Temperature throughout the cargo oil discharge operations. During discharging, the monitoring of the cargo tanks not connected to the IGS shall be done carefully and more frequently. Watch the Temperature. (in case of heated cargoes) On completion of cargo discharge and before shutting down the IGS, increase the IG pressure in all oil cargo tanks sufficiently. (Allow for cooling down of Temperature inside cargo tanks).
During Ballast Voyage
Maintain the cargo oil tank pressure in all cargo oil tanks at a minimum 100 mmAq during the ballast voyage. Start IGS plant if required to raise tank pressure. However, if the Temperature was raised sufficiently at the discharge port, the above may not be generally necessary. Be aware that during a sudden drop in the ambient Temperature, it may cause air to enter the cargo oil tanks through the P/V valves, increasing the O2 level, thereby causing an explosive atmosphere inside the cargo tanks. Leave individual cargo tanks IG supply valves open during the ballast voyage and monitor the IG main line pressure from the cargo control room or the bridge.
Cargo Loading Operation
Ensure that the O2 level in all cargo oil tanks is less than 8% and that the tank pressure is minimum 100 mmAq upon arrival at load port, using Double Hull (D/H) Operational Record Voyage record of COT Oxygen / H2S content. In specific ports, the maximum oxygen content of Inert Gas in the cargo tanks maybe 5% to meet particular safety requirements, such as the operation of a vapor emission control system. In such cases, follow terminal requirements. For special requirements for arrival tank atmosphere conditions and limitations, prior loading, follow applicable local port/terminal requirements. It is not required to operate the IGS during cargo oil loading operations.
Secondary Venting
The subject of secondary venting and the capacity of the equipment is occasionally questioned by vetting inspectors. Vessels fitted with the Full Flow PV / High-Velocity Vent Valve(HVVV) comply with the requirements as required by SOLAS Chapter II-2 Regulation 11, Sections 6.3.2, 6.3.4 & 6.4. The primary venting system on vessels is via IG main mast riser, protected by a full flow P/V Breaker. Secondary venting is achieved via. Individual cargo tank P/V Valves which have an individual full flow capacity.
PV (Pressure Vacuum) / HV (High Velocity) Valves
The maintenance of cargo tanks PV / HVVV is to be carried out as per the PMS. Such a record of maintenance using Cargo Tank PV Valves and related correspondence is to be filed on board.
During Loaded Voyage
Cargo tanks shall be maintained at positive pressure. Under normal conditions, it is not necessary to run the IGS during the loaded voyage. Moreover, due to the hydrocarbon generation, the level of oxygen inside the tanks would be well under the levels before loading (empty tank conditions), provided no ingress of air has occurred. If vapor segregation is not required, the tank pressures are connected to the standard IG line and can be monitored from the central location (Navigation Bridge or Cargo Control Room).
Be aware that during a sudden drop in the ambient Temperature, air may enter the cargo oil tanks through the P/V Valves on each Cargo Oil Tank, increasing the O2 level. For the sake of exercising due diligence, on behalf of the carrier, on completion of loading, the IGS Record of Pressure shall be left in constant operation, to carry out voyage recording of Cargo Tank IG Pressure. Where there is vapor segregation required to be maintained between grades, the Segregated tanks pressure shall be monitored frequently (not greater than four hourly intervals). This interval shall be reduced, depending upon the nature of cargo (tendency to gasify at maintained Temperature), percentage of filling, and Temperature.
Handling Troubles & Failure Of IGS During Discharging / COW Operations
If the Inert Gas System(IGS) is malfunctioning during operations, the oil transfer operations must be suspended immediately, and not resume until the IGS is in good working condition (or) an alternative Inert Gas supply is provided. Such emergency action in the case of Failure of the Inert Gas System is required to maintain a positive pressure in the cargo or slop tanks. The inert gas main isolating valve should be shut. The terminal must then be informed as soon as possible.
Other Operations
To operate the IGS for Tank cleaning, Gas freeing, and Crude Oil Washing Operations, extra caution needs to be exercised in each procedure.
Records
The following records must be retained onboard for minimum 5 years:
- Operation Record of Inert Gas System
- Maintenance Record of Inert Gas System (Running)
- Maintenance Record of Inert Gas System (Docking)
Did you subscribe to our Newsletter?
It’s Free! Click here to Subscribe!
Source: Ship Business