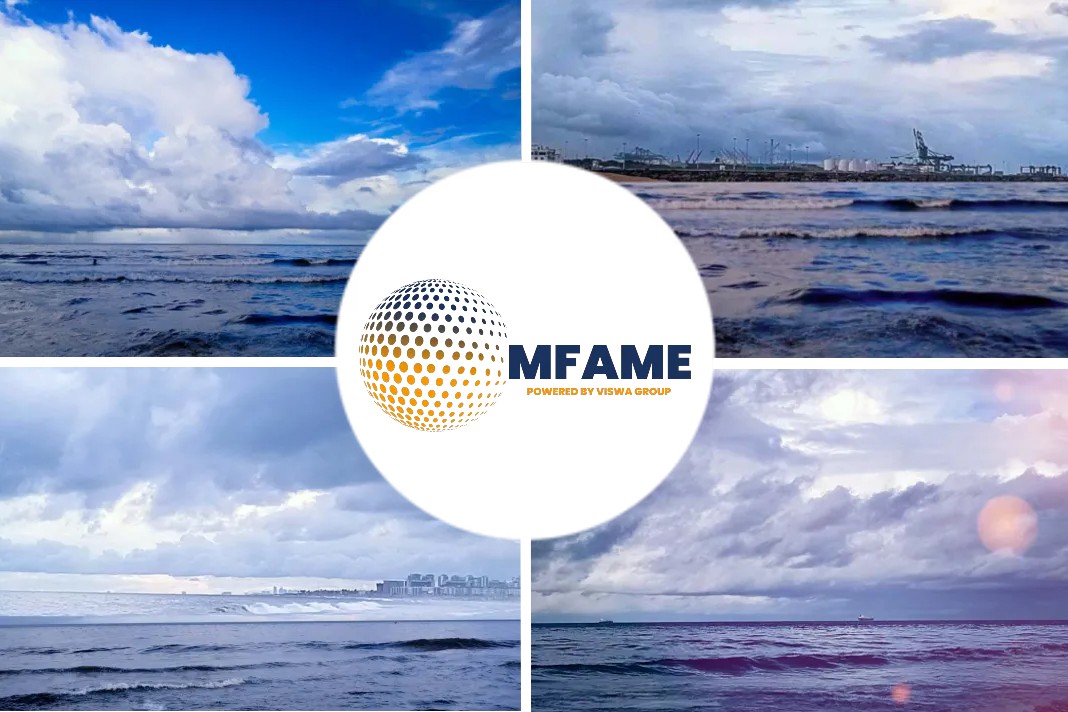
An oil tanker was tied off the south coast of the UK when an auxiliary room fire alarm went off, according to UK MAIB’s most current Safety Digest.
The incident
When the ship’s firefighting crew went to the engine room to investigate, they saw smoke coming from a seawater pump that was overheating. They stopped the pump, let it cool, and determined that there was not much damage.
A number of machines received cooling water from the pump. One of the ship’s engineers had shut off the valves to one piece of machinery three days prior to the event in anticipation of scheduled repair, but he was unaware that all of the other pieces of equipment had been similarly isolated.
When the valves were shut and there was no flow through the cooling pump, the cooling water had nowhere to go, which led to the mechanical seal’s slow overheating and production of smoke.
Lessons learned
- Communicate: Maintenance should be effectively planned and communicated. It is vital to consider the effects of isolation on running equipment that may not be directly related to the job at hand. The use of isolation logs and lock-out/tag-out notices can help engineers monitor the status of their systems and prevent mishaps.
- Aware: All of the human senses play a part in the detection of issues that electronic or mechanical sensors may fail to pick up. The application of touch, smell, sight and sound while moving through space are powerful tools in the armoury of a watchkeeping engineer and provide early warning of a developing problem.
Did you subscribe to our newsletter?
It’s free! Click here to subscribe!
Source: Safety4Sea