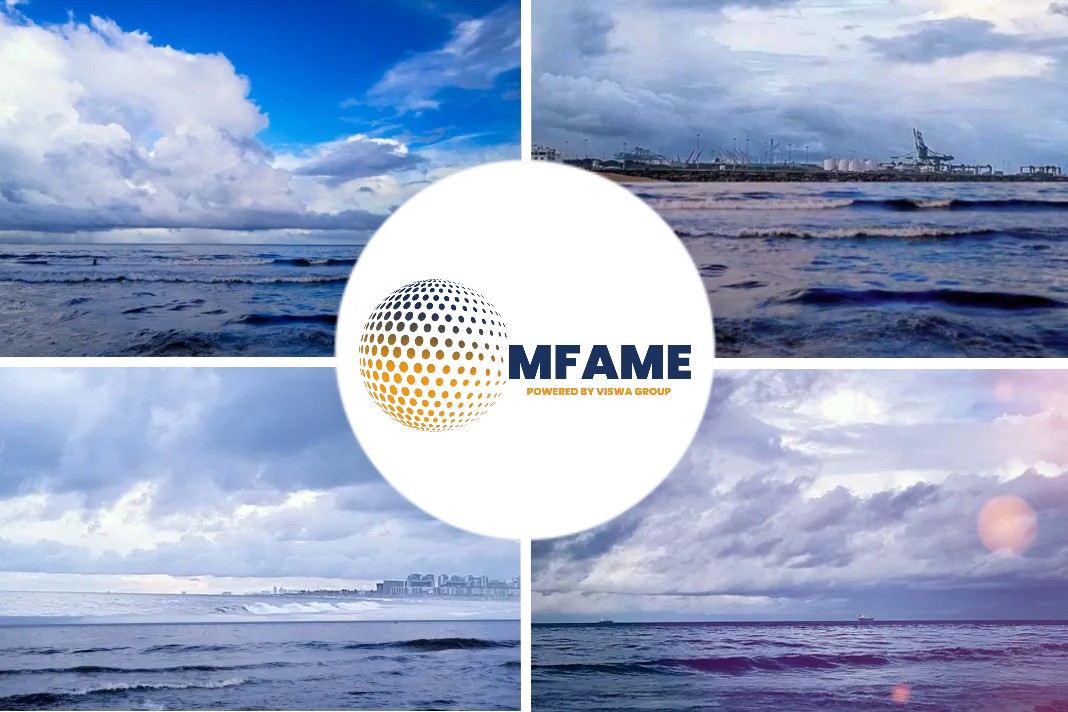
As American companies recalibrate the risks of relying on Chinese factories to make their goods, some are shifting business to a country far closer to home: Mexico. The unfolding trend known as “near-shoring” has drawn the attention of no less than Walmart, the global retail empire with headquarters in Arkansas, reports The Japan Times.
The contours of global trade
Early in 2022, when Walmart needed $1 million of company uniforms — more than 50,000 in one order — it bought them not from its usual suppliers in China but from Preslow, a family-run apparel business in Mexico.
It was February 2022, and the contours of global trade seemed up for alteration. The worst pandemic in a century had upended shipping. The cost of transporting products across the Pacific had skyrocketed, and ports were choked with floating traffic jams — a stark indication of the dangers of depending on a single faraway country for critical goods.
Among multinational companies, decades of faith in the merits of making things in China had come under scrutiny, especially as animosity intensified between Washington and Beijing.
At his office in Mexico City, Isaac Presburger, director of sales at Preslow, took Walmart’s order as a sign of his country’s evolving role in the economy, and the opportunities that flow from sharing the same side of the Pacific with the United States.
“Walmart had a big problem with their supply,” Presburger recounted. “They said, ‘OK, Mexico, save me.’”
Basic geography is a driver for U.S. companies moving business to Mexico. Shipping a container full of goods to the United States from China generally requires a month — a time frame that doubled and tripled during the worst disruptions of the pandemic. Yet factories in Mexico and retailers in the United States can be bridged within two weeks.
“Everybody who sources from China understands that there’s no way to get around that Pacific Ocean — there’s no technology for that,” said Raine Mahdi, founder of Zipfox, a San Diego-based company that links factories in Mexico with American companies seeking alternatives to Asia. “There’s always this push from customers: ‘Can you get it here faster?’”
During the first 10 months of 2022, Mexico exported $382 billion of goods to the United States, an increase of more than 20% over the same period in 2021, according to U.S. census data. Since 2019, American imports of Mexican goods have swelled by more than one-fourth.
In 2021, American investors put more money into Mexico — buying companies and financing projects — than into China, according to an analysis by the McKinsey Global Institute.
China will almost certainly remain a central component of manufacturing for years, say trade experts. But the shift toward Mexico represents a marginal reapportionment of the world’s manufacturing capacity amid recognition of hazards — from geopolitical realignments to the intensifying challenges of climate change.
“It’s not about deglobalization,” said Michael Burns, managing partner at Murray Hill Group, an investment firm focused on the supply chain. “It’s the next stage of globalization that is focused on regional networks.”
That Mexico looms as a potential means of cushioning Americans from the pitfalls of globalization amounts to a development rich in historical irony.
Three decades ago, Ross Perot, a business magnate then running for president, warned of “a giant sucking sound going south” in depicting Mexico as a threat to American livelihoods.
“The reality is that Mexico is the solution to some of our challenges,” said Shannon O’Neil, a Latin America specialist at the Council on Foreign Relations in New York. “Trade that is closer by from Canada or Mexico is much more likely to create and protect U.S. jobs.”
Given that the United States, Mexico and Canada operate within an expansive trade zone, their supply chains are often intertwined. Each contributes parts and raw materials used in finished goods by the others. Cars assembled in Mexico, for example, draw heavily on parts produced at factories in the United States.
Overall, about 40% of the value of Mexico’s exports to America consist of components made at American plants, according to a seminal research paper. Yet only 4% of imports from China are American-made.
A Walmart representative described the company’s interest in Mexico as part of an effort to make its supply chain less vulnerable to troubles in any one region.
For now, Mexico lacks the capacity to assume China’s place as the dominant supplier of a vast range of goods.
At Preslow’s factory, about 50 miles north of Mexico City, 200 seamstresses leaned over clattering sewing machines on a recent morning, stitching garments amid the strains of Mexican folk music. Local designers sat in front of computer screens, conjuring new creations.
Yet the storage shelves were piled with bolts of synthetic fabric, nearly all of it made in China.
“All the basic materials are still imported from China, because you don’t have the suppliers here,” Presburger said. “The fabrics I use are impossible to get in Mexico.”
Closer to home
In a bedroom community north of Dallas, Jose and Veronica Justiniano were also dependent on vital goods from Asia and eager to find a vendor in the same hemisphere.
The couple ran a small business, Veronica’s Embroidery, out of their home. They supplied restaurants, construction companies and maid services with uniforms for their employees.
Born and raised in El Salvador, they had left behind a horrific civil war to forge comfortable lives in the United States.
Jose Justiniano, 50, landed first in Los Angeles, where he worked as a janitor at the Beverly Hills jail and then as a billboard installer. After moving to Dallas, he got a job at an auto-parts plant and eventually rose to supervisor, gaining expertise in machinery. Veronica Justiniano, 54, worked as a home aide to an aging couple.
In 2018, the couple bought their first embroidery machine, installing it in an upstairs bedroom. The next year, they secured their most important customer — Gloria’s Latin Cuisine, a chain of 22 fine-dining restaurants in Dallas, Houston, San Antonio and Austin.
The Justinianos bought uniforms from a company that imported them from Asia. Then they used their machines to embroider the logos.
Their distributor maintained huge stocks of inventory at warehouses in Texas, typically delivering within a day. But as the pandemic intensified in 2020, days turned into months. The Justinianos were late in their own deliveries, a mortifying threat to their business.
Jose Justiniano hurriedly sought another supplier.
“The only way was Mexico,” he said.
They eventually entrusted much of their business to Lazzar Uniforms, a family-run company in Guadalajara, a booming city about 350 miles northwest of Mexico’s capital. Lazzar’s commercial director, Ramon Becerra, 39, was eager to gain a crack at the enormous market to the north.
“We know the U.S. is the future for us,” Becerra said.
The Justinianos’ American distributor operated in bulk, selling only what it had in stock and providing no custom work. Lazzar, on the other hand, beckoned as a design shop and apparel factory in one.
Becerra’s team conferred on the particulars of what the Justinianos desired: a light fabric that vented away moisture, providing relief from the heat of the kitchen. The two companies were able to communicate easily by phone and video without having to navigate a time difference.
They started small, with a few dozen chef’s jackets. By September 2021, Veronica’s Embroidery was purchasing 1,000 linen shirts in a single order, at prices close to what its previous distributor charged for imports from Asia.
On a recent morning, Becerra hosted Jose Justiniano at his factory in Guadalajara. The two men discussed a potential new partnership in which Lazzar would set up a warehouse in Texas, with Justiniano handling American distribution.
“This year has been a wake-up call for the U.S.,” Justiniano said. “We have to reconsider where we get our stuff made.”
A troubled legacy
The biggest impediment to Mexico’s reaching its potential as an alternative to China may be Mexico itself.
Its president, Andres Manuel Lopez Obrador, has neglected the nation’s infrastructure, including its ports.
Even Presburger, an enthusiastic promoter of his country’s industrial virtues, concedes that Mexico will struggle to amass the scope of China’s manufacturing capacity.
He recalled his first trip to China to look for fabric more than a decade ago. The scope of production left him astonished, with monumental spinning mills alongside specialized dying operations.
“The sheer size of the factories there is crazy,” he said. “I don’t think there’s a way back from that. It’s not going to be easy.”
Inside his factory, he displayed a popular item, a black bomber jacket adorned with an elaborate and colorful pattern. The zipper was made in Mexico, as was a skull-shaped ornament that pulled it. But the rest of the components — the fabric, the thread, the liner — were all made across the Pacific.
Still, a shift is palpable.
Near Preslow’s plant, an enormous factory makes as many as 6 million buttons per day, employing about 1,500 people. The company, Botones Loren, has seen its sales grow by nearly two-thirds over the past year. Its customers — international brands such as Armani and Men’s Warehouse — are shifting orders from China, said CEO Sony Chalouah.
“They think that the U.S. will continue to be fighting with China,” he said. “They want to not depend on China.”
The geopolitical realignment
Some within the apparel industry anticipate that Mexico’s appeal will fade as normalcy returns to the global supply chain.
Shipping prices have sharply declined over the past year. China has begun loosening COVID-19 restrictions. Chinese apparel makers are aggressively courting business by offering steep discounts, according to Bernardo Samper, a longtime New York sourcing agent.
“At the end of the day, everything is driven by pricing,” he said.
Yet within Mexico, businesses are counting on continuing acrimony between the United States and China.
The Trump administration imposed steep tariffs on hundreds of billions of dollars of Chinese imports. President Joe Biden has continued that policy, while adding measures that seek to deny China access to technology.
Washington has accused the Chinese government of genocide in its brutal repression of the minority Uyghur community in the western Xinjiang region — a major source of cotton. Any company buying clothing made in China risks accusations of exploiting Uyghur forced labor.
Russia’s invasion of Ukraine and its deepening ties with China have amplified the sense that the world is dividing into distinct camps of allies and enemies.
Companies need reliable supply chains.
Lectra, a French company that makes machines that cut fabric into pieces for the apparel industry, has seen its sales in Mexico and Central America grow by nearly one-third over the past year.
“What is driving this near-shoring is basically the situation between the U.S. and China,” said the company’s commercial director for the region, Carlos Sarmiento.
“It’s not that China is going to disappear from the American market,” he added. “It’s that there is more openness to look at Mexico and Central America as an alternative rather than depend entirely on China.”
Did you subscribe to our daily Newsletter?
It’s Free! Click here to Subscribe
Source: The Japan Times
Can you be more specific about the content of your article? After reading it, I still have some doubts. Hope you can help me. https://www.binance.info/bg/join?ref=T7KCZASX